What Is A Fleet’s Maintenance Maturity Scale?
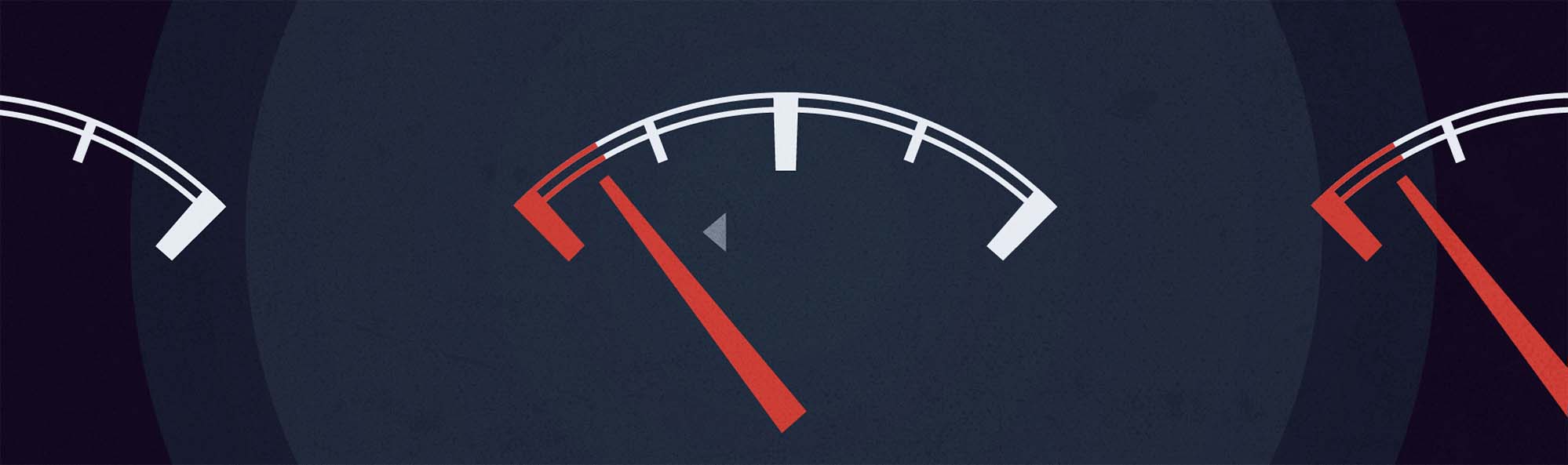
Some ideas make so much sense that it doesn’t seem logical not to use them. The Maintenance Maturity Scale is a good example. It’s a gauge for measuring maintenance routines that lets you assess how well your crew handles maintaining your fleet’s maintenance. The Maintenance Maturity Scale is a common-sense approach to a manufacturing standard Winston Ledet developed. A hands-on maintenance management whiz who wrote the Manufacturing Game, Ledet understands how to maximize accuracy and efficiency when it comes to fleet upkeep.
The Concept
The idea behind the Maintenance Maturity Scale is that businesses—like manufacturers or fleets—deal with repairs in common, specific ways. Each way of handling maintenance has its own spot on the scale. Each level indicates how efficiently a crew is at keeping fleets running smoothly. In other words, the scale is a good gauge of how mature your practices are. It also serves as a roadmap to help you move up to the next level.
Maintenance Maturity Scale Levels
Reactive maturity is the bottom level of the Maintenance Maturity Scale. Fleets on this level handle maintenance by reacting when a truck isn’t working right. However, it’s more expensive to wait until a truck breaks down to have a tech look at it. First, you’ll have to pay for the repair. Second, the business loses money whenever there’s an unplanned out of service truck.
Preventive maintenance is the next level on the scale. It’s the level most fleets are at. By planning for maintenance, you avoid unscheduled downtime altogether. It’s also effective for catching problems early and fixing them before they become a bigger issue.
Predictive maintenance is the next level up after preventive maintenance. At this point, you’ll have the records to figure when truck parts will probably fail. A good history on each vehicle is helpful, but self-checking systems take predictive maintenance to another level. For example, it’s smart to perform regular oil changes and lubes. However, it’s useful for the driver to receive an alert when the oil level is low. Especially if a regular PM isn’t on the schedule soon.
Precision is the top level to strive for. Precision maintenance is defined as handling all aspects of a truck following precise instructions. That’s everything from operation to repairs and maintenance to fuel. It means operating the truck according to the manual and using the fuel specified by the manufacturer. It also goes for repairs, lubing, oil changes, balancing and aligning tires, and all other upkeep tasks done during PMs.
Avoid Slipping Back on the Scale
The preventive and predictive levels on the scale work together so well they could almost share one level. However, some fleets have a tough time staying on either level. It’s easy to forget PMs. Plus, when time or funds are short, it’s even easier to let maintenance go just this once. The problem is that once can turn into several times. Then, before you know it, you’re back on the first level at reactive maturity.
Some experts say achieving the precision level is the best way to avoid slipping back on the scale. Going by the book with parts and repairs is a great way to keep your fleet in top shape. However, you’ll also benefit from keeping up with preventive and predictive maintenance. There’s no better way to keep you on track with those levels than Fullbay software. You can use it to schedule routine PMs when it’s convenient rather than waiting for a breakdown. It also keeps track of vehicle history, building a matchless database that makes predictive maintenance a snap. Fullbay will take your fleet to a whole new level on the Maintenance Maturity Scale and keep it there.