Diesel Repair Shop Layout
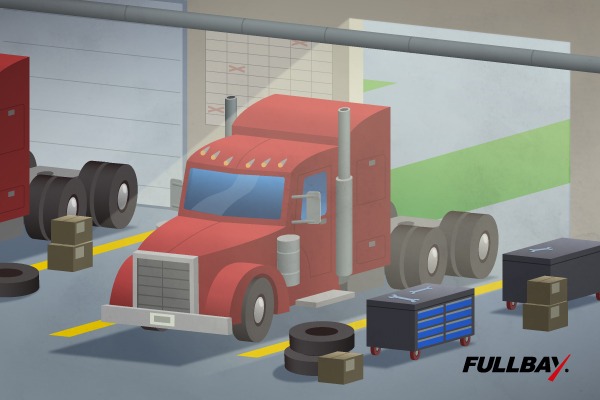
What does your dream shop look like?
Is it furnished with state-of-the-art equipment and tools? Does it extend into the distance, housing numerous bays and a warehouse full of parts? Or maybe it’s a small, two- or three-bay garage with just enough room to keep your most-used tools within reach.
Whatever your ideal heavy-duty repair shop looks like, there are a few details you can’t overlook. A diesel repair shop layout designed to maximize safety and productivity also improves profitability, as it gives your techs a clean, comfortable environment to work in. And we haven’t even touched on the bold impression a well-organized shop can make on customers.
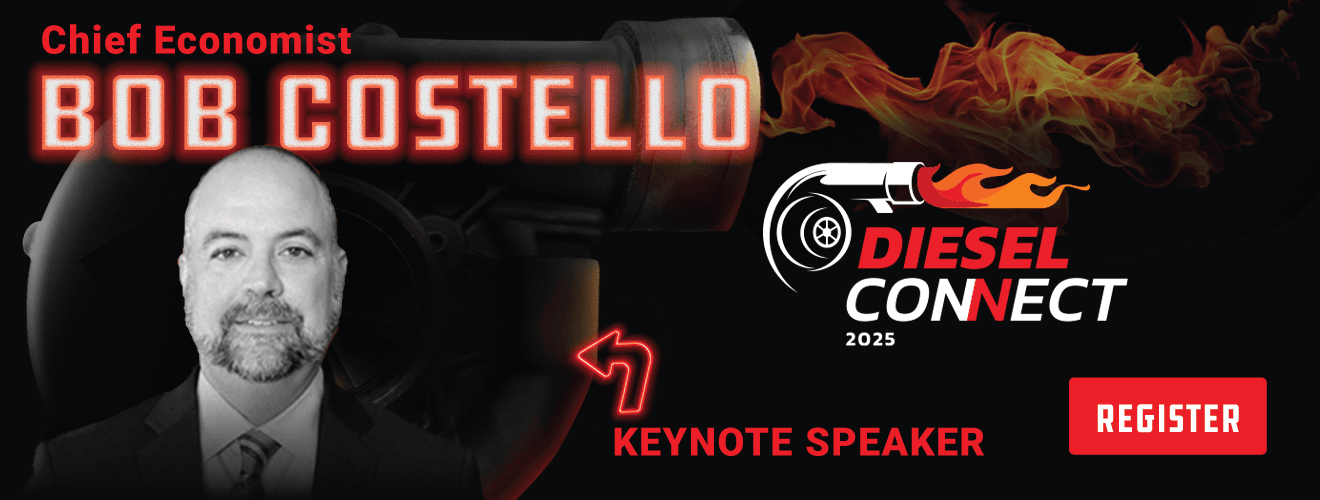
We aren’t design experts and we have no idea what your personal preferences are, so we aren’t going to fling down any fancy floor plans for you to use. What we are going to do is explore the basic elements that will improve any diesel repair shop layout.
Let’s get started.
The Outside Matters
Before jumping into dreams of paint schemes and repair bays, remember that your shop technically starts on the outside. Make an exterior that is visually appealing but practical, too. Whether you’re building a new shop or optimizing an existing building, check your city’s local building and zoning codes to ensure your shop complies. This is critical, as some areas restrict things like how many garage doors can face the road. That kind of restriction is definitely going to affect your internal layout!
Here’s a tip we wish all shop owners followed: Plan for plenty of parking. You’ll need room for customers and visitors, as well as space to store tractors and trailers waiting for work or that have been worked on. Nothing is going to aggravate a potential customer more than waiting for you to clear a space for them to park in.
Keep the outside of your shop organized and free from clutter, too. It’s logical to locate compressors outside to keep the noise level down, but place them to the side or the back of your building rather than out front, if possible. Even outside, the noise is just as loud and possibly aggravating.
Organize any equipment outside the building, and keep it out of the way of foot traffic to avoid tripping hazards. Plan for a shipping and receiving dock close to where you keep your inventory. That should also be along the side or the back, if possible, to improve efficiency as well as reduce congestion in your reception area and workspaces.
One element we don’t see discussed often is your region’s weather. As we noted in our piece about signs, everything you place outside is subject to the elements. If you live in a place with high winds or hurricanes, for instance, you likely don’t want fabric awnings that can be ripped away in a gale. Places with lots of rain will need adequate coverage, often with materials treated to withstand moisture. Does the sun beat down on your building? You can look forward to repainting more often as the colors fade.
Internal Layout
We don’t need to tell you twice to pay careful attention to your interior. But you should have some idea of where you want things to be, and how long it will take you or your staff to reach them.
For example, see how long it will take you to walk between the bays and the parts room. There are two factors at stake here: First, you don’t want your techs hiking back and forth all day when they should be working. Second, every three-minute walk to the parts room usually turns into at least a six-minute round trip. Add that up by a few trips a day, followed by trips to the break room (if you have one) and bathroom, and suddenly your layout – however expansive it may be – is cutting into your efficiency and your profit.
Your best bet is to follow in Goldilocks’ footsteps: Not too big, not too small. Before you commit to any design, make sure you take it for a test drive (well…a test walk). And hey, remember that if you get Fullbay, your techs won’t need to walk to the service desk every other hour.
Service Bay to Technician Ratio
You need enough service bays to accommodate the amount of work you’re going to do. So here’s a secret: A 1:1 bay-to-tech ratio isn’t enough.
Why?
It restricts your techs to working on one vehicle at a time, and that’s a waste.
Think about it. What happens when a job gets held up waiting for a part? If you’ve only got one bay per tech, then once a vehicle is in that bay, a tech is committed to working on it. That’s well and good if you’ve got everything you need for that particular job, but what if you don’t? You’ll need to either leave the truck in the bay, losing that valuable workspace, or lose valuable time moving the truck and finding a place to put it (another point in favor of decent parking, by the way). This leads to bottlenecks.
A good rule to follow in figuring out how many bays you need is planning for 1.5 to 2 bays per tech. Instead of moving a truck or letting a vehicle sit until a part arrives, extra bays allow technicians to start work on the next job. It also leaves the job-in-progress ready to go, so techs can quickly pick up where they left off.
Invest In Proper Equipment Storage
Your shop’s equipment represents a huge investment; you may have spent as much or more on your machinery as you do on the rent or mortgage of your building.
But you aren’t using all that equipment all the time. Which means you need a space to store it.
Large tools, jack stands, and diagnostic computers can get in the way when you’re not using them. Still, technicians need these items nearby, so they don’t have to waste time looking for them or trekking across the shop to retrieve them. Keep your equipment stored close to the service bays, but in a space that is easily organized and will keep things out of the way.
Train all of your techs to put equipment away when they’re done using it. A wrench left out here, or a jack stand left alone there, may not seem like a big deal, but multiply that by the amount of tools you have and the techs employed and you may be looking at a cluttered mess. When you hire a newbie, stress that they’ve got to place tools back where they find them.
Your Lighting Is Your Lifeline
You can’t work without good lightning.
Well, you can try, but we don’t recommend it.
Natural lighting is generally best, so install skylights in the ceiling and full-length doors with lots of windows on them. Painting your walls white will help reflect that natural light even on gray days – and it also brightens up the shop somewhat, which can lead to lower electric bills.
You’ll still need interior lighting, though. Instead of trying to place a couple of large, bright lights where shadows from pillars and equipment won’t cast a shadow, install smaller LED fixtures at close intervals throughout your shop. They’ll spread the light more evenly around the work area, and the bulbs will last longer than fluorescents.
Don’t Forget To Clean
You know what else you’ll need to store? Cleaning supplies. Keep mops, brooms, rags, and cleaning fluids of all sorts handy. Along with training your techs to put their equipment away, make sure they clean up their workspace afterward. You may want to install a locker in each bay so that a tech can quickly tidy up after performing a repair.
Your Layout Matters
Whether you’re building your business from the ground up or adapting an existing building, a well-planned diesel repair shop layout is crucial to a successful business. A thoughtful layout helps techs work more efficiently, saves you money on utilities, and reduces spending on lost and misplaced tools and equipment. Work flows better, your shop looks great, and your bottom line gets a boost.
We think that’s a winning combination all around.