How to Prevent Wheel-Off Conditions
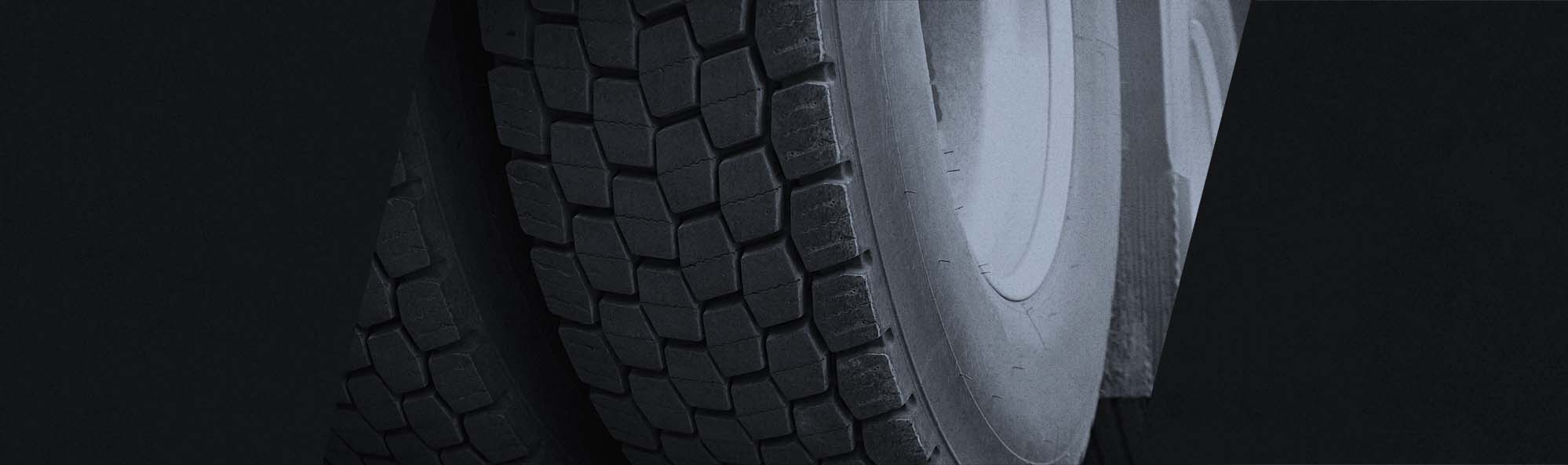
Problems with wheel separation are an under-the-radar issue. Lost wheels don’t always cause a crash. When they do, though, that detail does not always get pinpointed or reported. Although most cases of wheel separation don’t get reported, industry experts believe that wheel-off incidents happen daily. Wheel-off conditions are more than a safety concern. They’re a bottom-line issue, too. Repairing wheel separation involves taking a truck out of service as well as the cost of parts and labor. Taking preventative steps will nip wheel-off conditions in the bud, boosting safety along with profits.
Wheel-Off Conditions Causes
Knowing what causes wheel-off conditions is the first step in stopping them. According to the National Transportation Safety Board, the top reasons semi wheels separate are bearing failure or wheel fasteners with too much or too little torque. Delve a little deeper and you’ll find poor maintenance at the bottom of both those causes.
Inspections and Maintenance Help Prevent Wheel Separation
Essentially, in-depth inspections and stepping up your maintenance game will go a long way to thwart wheel-off conditions. Of course, thorough pre and post-trip checks are crucial.
Furthermore, certain wheel components should be inspected monthly, quarterly, and annually. Once a month, check the hubcaps and back area of hubs for leaking and damaged gaskets or seals. Once per quarter, do a touch-test to check for uneven spinning of the wheels or too much endplay. Then, once a year, have a tech remove and clean the hub assemblies. He should examine all the parts during the process and replace worn or damaged pieces as well as install new seals during reassembly and repack the bearings with new lube, too.
Also, use correct lubrication. It must be made for wheel-ends. Look for a working temperature range between -20 and 325º F for grease. Additionally, synthetic and mineral oils have to meet API GL-5/MT-1 specifications or the SAE J2360 requirements.
It Takes a Pro
The margin for error is only about the width of two hairs. That’s why bearing and seal experts stress the importance of precision when adjusting bearings. Safe and accurate servicing require a properly trained tech with advanced education who’s been certified in wheel-end systems. A pro is familiar with the Technology and Maintenance Council’s RP 618 guidelines. They outline the different adjustments for different hub and wheel bearing systems. The instructions advise based on axle type and include steps like:
- initial and final nut torque
- initial and final back off
- jam nut torque
- nut size
- threads per inch
Other Preventative Measures
Besides adjusting and installing bearings correctly and using proper lubrication, there are a few other details that will help prevent wheel-off conditions. First, the area between the wheels and the hub must be completely contaminant-free. Clean away all rust, grease, and dirt before reinstalling a wheel.
Second, use a calibrated torquing tool to finish off fastening nuts after manually tightening them. This will ensure proper torque without overdoing it which can stretch the stud too far, resulting in incorrect clamp load.
Finally, it’s not always vital to replace parts when performing wheel-end maintenance. No, components like bolts, nuts, and other parts won’t last forever. However, unless there’s thread damage or they’re corroded beyond cleaning and repair, you can reuse a lot of them. Sometimes you can reuse bearings, though thorough inspection is essential. Even the smallest burr or nick is reason enough for replacement.
Plus, though we’ve mentioned it before, it’s worth saying again: PMs and maintenance are vital for avoiding wheel-off conditions. If you need help staying on track with these two essential tasks, Fullbay software can help. It will not only keep you on top of schedules and repairs, it will also keep track of vehicle history and parts inventory, too. And that’s just the beginning of what Fullbay can do. Want to know more? Fill in your info below and request a demo today.