What Is an Inventory Management System?
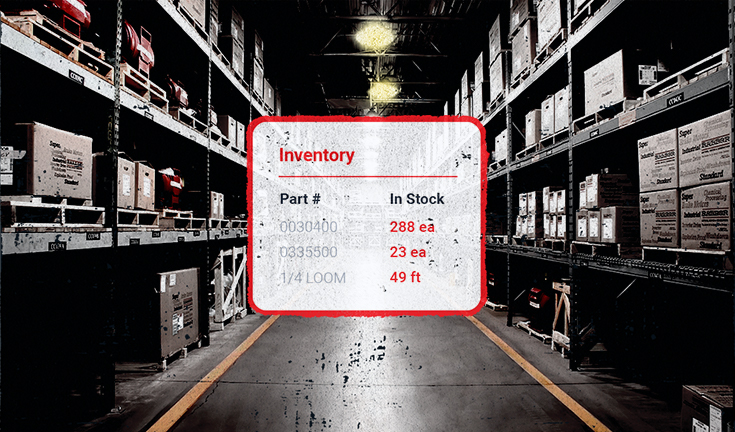
Without a smart approach to inventory management, any heavy-duty repair shop will struggle to reach its full potential. If you want to improve your business’ inventory strategy, you’ll need to start by answering one simple question: “What is inventory management system?”
No, hold on: we meant “what are inventory management systems?” You’ve gotta understand, it’s been a crazy couple of weeks here at Fullbay HQ. The office coffee maker broke down, and we didn’t have the parts we needed to fix it—now, it’s been days since we’ve had a steady supply of caffeine! Man, it would be nice if we had a program to keep track of things like that.
But in the meantime, we’ve got a job to do. Keep reading for our in-depth answer to that age-old question: “what is inventory management systems, or an inventory management system, or whatever?”
What Is an Inventory Management System?
Before we get into how inventory programs can make life easier for you and your techs, we should take a moment to define “inventory management system” as a term. Naturally, these systems are all about tracking your shop’s inventory—that is, the collection of components it uses in repairs and sells to customers.
Since you can’t complete jobs without these parts, it’s always a good idea to monitor the number of components you have in stock and their location in your shop. Of course, this process is called “inventory management.”
At this point, we’ve explained two of the three words used in the phrase “inventory management system,” so let’s go for the hat trick. An inventory management system is the method a shop uses to keep track of its stock levels, service orders, and deliveries. These systems often take the form of dedicated programs, but any type of inventory tracking can fall into this category—even keeping track of parts manually via notebooks counts as a type of system. (This doesn’t mean managing inventory by hand is in your shop’s best interest, but we’ll get into that later.)
Why You Need an Inventory Management System
If your heavy equipment shop doesn’t have a software-based inventory management system in place, you’re missing out on some serious benefits. Modern inventory management systems can help shops with:
- Cost efficiency. Running out of parts can harm your shop, but so can the carrying costs associated with excess inventory. With the right inventory management system, you can avoid both of these problems.
- Improved accuracy. When your order management and inventory tracking processes are fully automated, human error isn’t something you’ll need to worry about.
- Time management. If you’re able to automate repetitive inventory tasks, your workers won’t have to spend time on them. Instead, they’ll be able to focus on completing jobs and providing high-quality customer service.
- Scalability. Choosing a scalable inventory management system will allow you to stick with the same program indefinitely—no matter how many parts you have in stock.
How Does an Inventory Management System Work?
Now that you’ve answered the question “what are inventory management systems?” and found out why inventory management systems matter, let’s take a closer look at how these systems work. Inventory management software can take care of many different tasks around the average heavy-duty shop, including:
Inventory Tracking
Your shop needs to be capable of tracking parts, but this task isn’t easy for businesses that still rely on “traditional” inventory management methods. Since these systems are based on human record-keeping, you could easily lose track of parts if an employee misplaces (or steals) them.
Fortunately, that won’t be an issue when your shop has access to an automated inventory system. These systems allow you to monitor part movement (including inbound and outbound movement) in real time, ensuring they won’t go missing.
Automated Reordering
If you’re juggling what feels like a million diesel truck repair jobs, keeping a close eye on your shop’s part levels can be tricky. But if you don’t do that, it won’t be long before your jobs hit a wall due to out-of-stock components.
But you don’t have to track this information alone—at least, not when you have the right inventory management system in place. Your shop’s software should be able to monitor part levels until they hit a certain threshold. At that point, it should automatically send you a reminder letting you know it’s time to order more parts.
Reporting and Analytics
While you can partially optimize inventory levels by only ordering parts when your shop needs them, this method isn’t infallible by itself. If you order too many replacement components at this time, these parts could sit on a shelf indefinitely.
That’s why the best inventory management systems provide reporting and analytics features. With the help of these capabilities, you’ll be able to forecast your shop’s parts demands based on hard numbers—and order the exact number of components you need in the process.
Integration with Other Systems
Admittedly, “working with other programs” isn’t a “task” in the same sense as tracking inventory or sending reorder reminders. Still, it’s hard to ignore the fact that modern-day business software rarely operates in a vacuum.
With that in mind, your automated inventory management system must be compatible with other programs around your shop. Ideally, this program should be able to keep things running smoothly by integrating with your business’ accounting, CRM, and ERP systems.
Types of Inventory Management Systems
Finally, you’ll want to get familiar with the three basic types of inventory management systems before purchasing one of these programs:
1. Manual Inventory Systems
As their name implies, manual inventory systems rely on “old-fashioned” part tracking methods such as counting by hand or using spreadsheets. If your shop already uses these strategies to manage its inventory, it may be tempting to keep doing what you’re doing—but this really isn’t a great idea.
The fact is, manual inventory systems are less efficient than just about any other approach to parts management. Because of that, your business should adopt an automated inventory management system as soon as possible.
2. Barcode Systems
As their name implies (again?), barcode systems manage inventory by using barcodes to track a shop’s parts. With one of these systems, your employees will scan parts whenever they move from Point A to Point B.
Since they don’t rely on human input beyond scanning, barcode systems are a far better option for your shop than manual inventory systems. But if your inventory management system is “locked” to a specific workstation, your employees will still waste time walking back and forth to that computer.
3. Cloud-Based Systems
As their name implies (ugh), cloud-based systems allow your workers to access inventory information via the cloud. That means they can get this information wherever they are—whether they’re using a workstation in your shop or a mobile device. As a result, these systems are more efficient than any other form of inventory management.
Fullbay: The Industry’s Best Inventory Management System
If you’ve ever wondered “what is inventory management system?” one thing’s for sure—you probably haven’t had your morning coffee yet. But if you’re asking “what are inventory management systems?” we hope this article has helped you learn about these programs and how they can improve your shop’s workflow.
When you’re shopping for inventory management software, find a program that can track parts with barcode scans, give your workers easy access to inventory information, and remind you when you’re running low on components. To enjoy these features and more, make Fullbay part of your shop’s inventory management strategy.
At Fulbay, we’re proud to offer the best inventory management software in the heavy-duty industry. Get started by schedule demo (sorry, scheduling a demo) today!