Need a Lift? A Quick Rundown of Things to Know
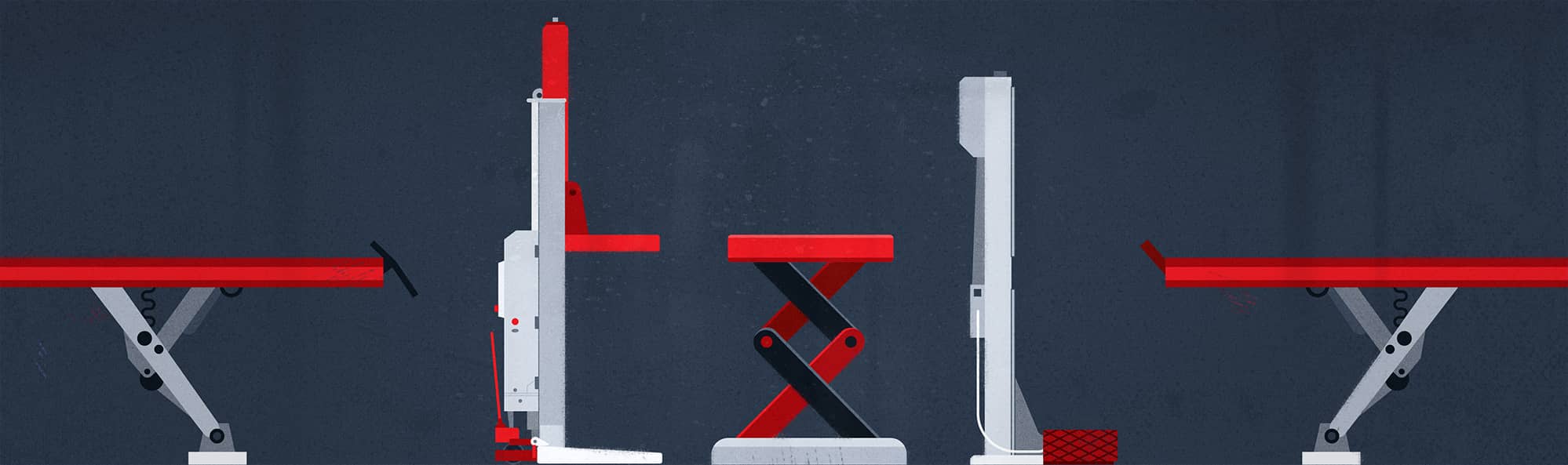
Ever thought about getting a lift for your shop?
If you’ve landed on this article, chances are you’ve at least kicked the idea around. Your shop may be operating just fine without one, but bringing a lift into play can change your whole operation.
Still, it’s not something to undertake on a whim. We know a lot of shops that are presently thinking about investing in lifts, so we talked with a few experts on the matter to get their opinions and advice:
- Matthew Morgan, EVP of Hoffman Services, Inc.
- Paul D. Feldmen, Director of Marketing at Stertil-Koni
- Peter Bowers, Technical Sales Support Manager at Stertil-Koni
These three gentlemen fielded an array of questions and shared years of wisdom with us. Buying a lift for your shop is going to take time and thought, and obviously you aren’t going to learn all of it from one article—but we’d say this is a good place to start!
SHOULD I GET A LIFT?
“This is a question we routinely field,” says Matthew. “The operative word is invest.”
And make no mistake, a lift is typically a sizable monetary investment. Then again, so is any other tool you’re going to use during the course of business. All three of our experts encouraged shops to look past the initial outlay of cash to see what their return on investment might be.
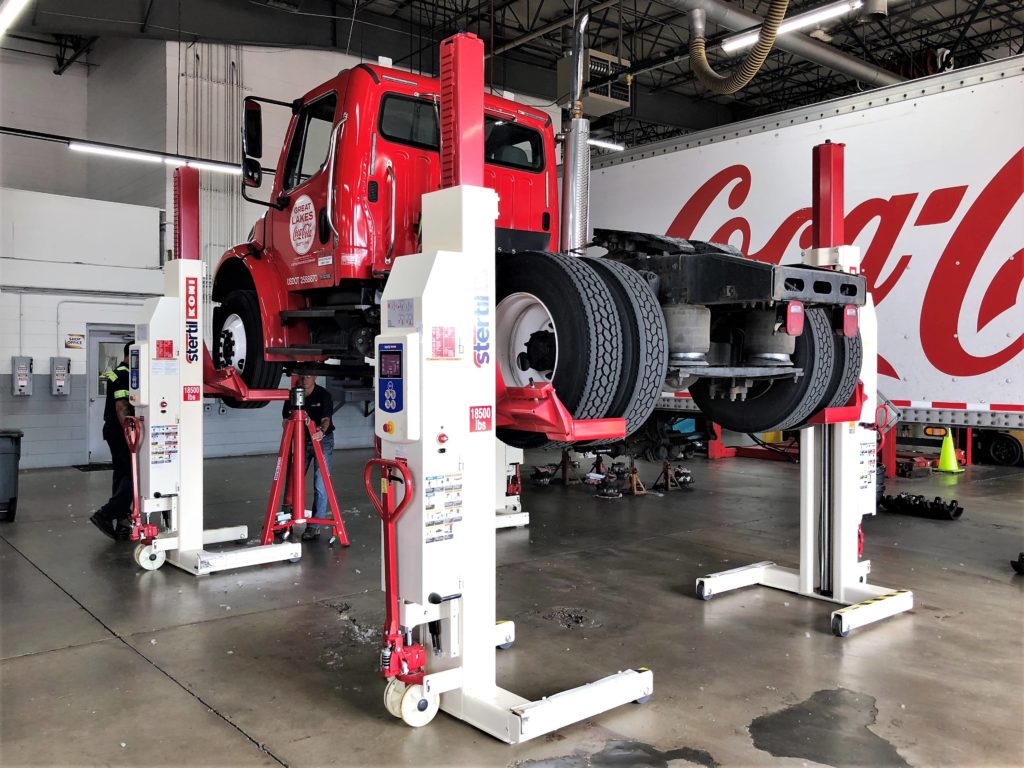
We’ll take a closer look at aspects of that return below, but things like improved ergonomics and easier repairs can lead to found time and improved shop morale. Consider being able to see serviceable items while on your feet, in broad daylight, instead of being on your back on a creeper. This can quickly translate into more jobs completed and techs staying on in your shop for a longer period.
In short, a lift is a tool that will ideally improve a lot of things in your shop. But it isn’t a purchase you’re going to make on the fly. Some questions you can ask yourself:
- What kind of vehicles am I primarily working on?
- Will the lift help me work on another type of vehicle, and will I need to get training for my techs to do so?
- Do I have the space for a lift?
- What kind of internal infrastructure do I need to operate the lift?
HOW CAN A LIFT BENEFIT MY SHOP?
The right lift makes everyone’s job easier. At least, that’s the idea. But there are two key areas where a lift can really help a shop level up.
Productivity
“There’s a huge jump in productivity between people having to work on the floor and on their backs, or working at full height,” Peter says. “When you look at brake work, suspension work, taking out a transmission, or servicing an engine…when you have a vehicle on a lift, it’s a much smoother and quicker process.”
Think of the time your techs might spend squirming around underneath a truck. If they’re able to just lift the truck up and start work immediately, that puts them way ahead of the game already. They can go ahead and get started on a repair while the techs in another shop are still poking around with a flashlight trying to figure out the problem.
“If you’re working at a flat rate and need to turn jobs around,” Peter adds, “the lift provides a way to do that.”
Matthew recounts a story about selling a mobile column lift to a distributor that had a truck with an exhaust leak. Rather than flop down on a creeper and poke around bit by bit, they lifted the truck up, saw exactly where the pipe was leaking, and then measured, cut, and welded it up in a third of the time.
Being able to see everything at once, while standing up, he assures us, is “a real game-changer.”
Ergonomics
Vehicle lifts lead to much better ergonomics for the technician, reducing the likelihood of back strain. Employee safety is rightfully at the front of everyone’s mind, and the very nature of the job means a heavy-duty diesel tech is surrounded by heavy parts every day.
It’s much more comfortable to work standing up, rather than on your back or crouched.
“Good techs are a commodity,” Peter observes. “Shops are competing for them.” When you look between a shop where a tech works on his knees or on his back versus a shop that has state-of-the-art equipment like lifts, where he can get the job done much more quickly and safely, the tech is going to take a closer look at the shop with the lift.
The right ergonomics, as we noted above, can lead to better hires and better overall retention. And in the current environment, you want your good techs to stick around!
CAN I GET ANY OLD LIFT?
Not all vehicle lifts are the same. Yes, pretty much all of them will lift a vehicle off the ground, but there’s a lot of variation. Paul reminds potential buyers to look at the lifts that are most practical for what their shop does or what they want to do.
Some subcategories of lifts are:
- Heavy truck lifts
- Bus and vehicle lifts
- 4-post lifts
- Drive-on lifts
Before placing an order, you’ll need to think about what type of lift will bring the necessary value and versatility to your operation. For example, if you’re performing primarily PM work and oil changes and you need to turn things quickly, a platform lift might be for you. Your tech drives the vehicle onto the lift, you push the button, and the vehicle goes up in two minutes; you can drop the oil and get your brake line inspections and DOT inspections done at an ergonomic height.
On the other hand, an in-ground lift is ideal for wheel and suspension work. If you need to get the wheels off frequently, the in-ground lift gives you wheel-free operation quickly. You get the vehicle up, you get the wheels off with a wheel dolly, and you have unobstructed access to the bottom of the vehicle.

But an in-ground lift requires a certain amount of space (and the freedom to actually, y’know, make substantial structural changes to the building you occupy). If you don’t have that, you might be looking at a mobile column lift. It gives you complete access to the underside of the vehicle, and as their name suggests, they’re mobile. You can move them to different parts of the shop.
Here are some additional questions to ask yourself when looking at lifts:
- What types of repairs do you want to do?
- What weight capacity does your potential lift need?
- Does it have a robust mechanical locking system? (“If anything fails, the lift becomes a stand and nothing moves,” Paul says. As in, nothing falls.)
- Does the lift have synchronization so the front and rear lifting mechanisms are in constant communication with each other? (Front/rear weight can be quite different)
- Do you have the right ceiling clearance for the lift you want? (“Running a lift into a ceiling is a little counter-productive,” Peter adds.)
- Are you in a position where you can modify your building? (If you lease your space, that may limit your options; mobile columns may be your best bet.)
- Do you have the right power supply in your shop? (Some rural shops may not have three-phase electric power, which will also limit your lift options.)
IS THE LIFT ALI-CERTIFIED?
As you narrow down your lift options, make sure you’re looking at one that has the ALI “Gold Label” stamp of approval.
The Automotive Lift Institute, or ALI, is the watchdog of the lift business. It awards the Gold Label to lifts that have passed its rigorous testing, which includes “verification of the structural integrity of all the lift’s systems and components, proper function of its controls and load-holding devices, proper lowering speeds, and overload protection.”
Much like ASE is accepted in the industry for producing excellent techs, ALI is accepted for its exacting lift standards. If the lift you’re eyeing isn’t on the ALI list…you may want to reconsider.
HOW ARE YOU GOING TO MAINTAIN YOUR LIFT?
Unfortunately, we have not yet reached the level of technological advancement that will let us install a lift and leave it to operate in perpetuity without some kind of service. If you want it to operate correctly and remain a long-term asset to your shop, you’ll need to stay on top of its maintenance needs.
Yes, lifts need PM work, too! “These are heavy pieces of equipment,” Paul warns us. So before you open your wallet, ask yourself the following questions:
- What kind of warranty does it come with?
- Will the manufacturer or distributor send out a rep to service or repair it?
- Can that rep get out to you quickly, if necessary?
- Have you done your due diligence by reading online reviews and looking into the reputation of the manufacturer or distributor?
- Is the lift manufactured in North America or overseas?
That last question isn’t to deter you from finding an awesome lift made elsewhere. But if you do find a lift made in Wakanda, make sure Wakanda is willing to send a service rep overseas to make any necessary repairs on it.
“We routinely receive phone calls from people who purchased equipment and now have no one to contact for service,” Matthew remarks. “A little bit of preliminary legwork can go a long way.”
NEED A LIFT?
Obviously, the lift (or lifts!) you choose will depend on the space you have, what kind of work you do, and how much you can afford. And we’d like to caution you away from making any snap decisions. With that said, we hope this article has been a good primer for you and has given you the chance to zero in on what kind of lift your shop needs and can manage.
Good luck, and happy lifting!