The True Cost of Downtime
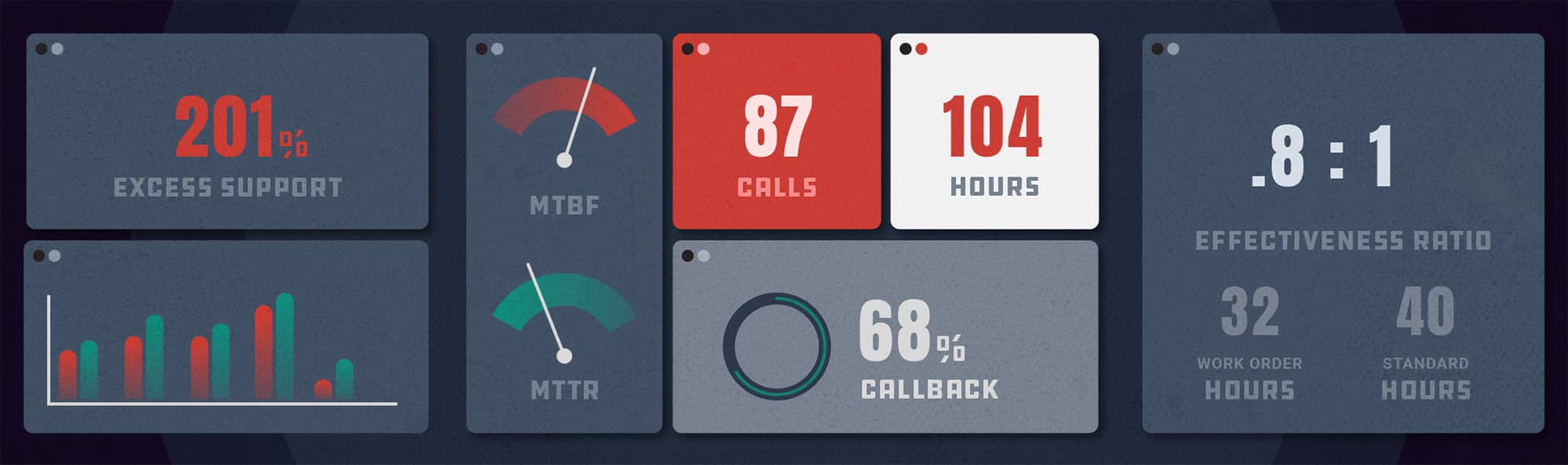
What it means to your service operation and your customers
When your fleet customers can tell you how unscheduled downtime impacts their bottom line, they aren’t just talking about the cost of repairs, towing, or replacement vehicles.
In over-the-road operations there is a measurable cost when a truck is not generating revenue. Depending on the freight being hauled, the distance, rates, and other factors, that loss of business can range from $450 to more than $750 each day. In delivery and vocational fleets there are similar losses when goods and services can’t be provided.
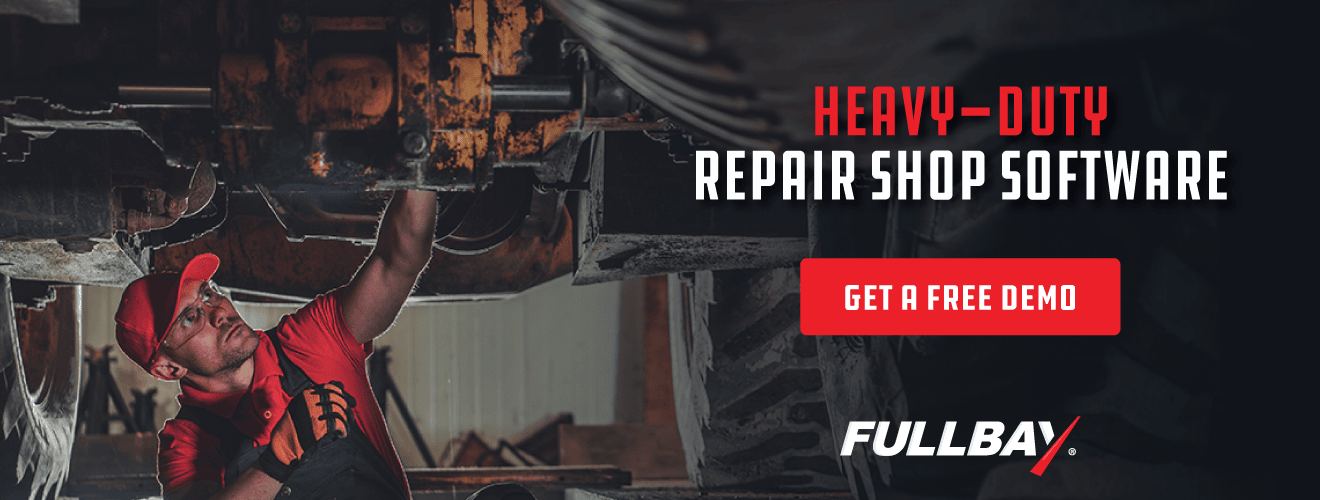
Across all types of commercial vehicle operations, there are also losses from unscheduled downtime that are measured in more than just dollars and cents. Sidelined drivers who are paid by the mile can be increasingly dissatisfied with equipment issues, leading to the need for time-consuming (and costly) recruiting and retention efforts. Perhaps most expensive in the long run is the impact of downtime on customer satisfaction and the resulting loss of business and missed opportunities for growth.
Recent industry data from repair and maintenance services and emergency roadside assistance provider FleetNet America and the Technology & Maintenance Council (TMC) of American Trucking Associations actually points to a rising number of breakdowns and unscheduled repairs. According to their reports, from the end of 2020 through the first quarter of 2021, fleets experienced an increase in unscheduled roadside maintenance.
The FleetNet America and TMC survey data shows that the number of miles between unscheduled roadside repairs reported by participating fleets fell 18.7% from Q4 2020 to Q1 2021, and were down 12.3% from one year earlier. If carriers running the average miles between breakdowns could reach best-in-class performance, according to FleetNet America, they would increase mileage between breakdowns by 89%.
Some downtime is unavoidable. Some downtime is even necessary.
All fleets will incur downtime. Beyond unforeseen component failures, some accidents, weather, and traffic issues are unavoidable. And some downtime is even important, and that’s precisely where heavy-duty repair shops can offer and implement valuable practices and capabilities, including:
- Inspections: Comprehensive inspection processes help find issues before they lead to unplanned downtime. It is especially beneficial to address concerns reported by drivers during pre- and post-trip inspections.
- Routine Maintenance: Timely preventive maintenance helps avoid breakdowns by keeping vehicles, systems, and components functioning properly, and can identify issues and limit downtime before major problems occur. While the costs of routine maintenance tend to be less than those for unscheduled service, industry surveys have shown that a preventive maintenance program can result in as much as 20% fewer downtime days.
- Campaigns: A preventive maintenance program can also include plans to replace or rebuild components at the end of their expected life cycle instead of waiting for a more costly failure and unnecessary downtime for repairs to occur.
- Telematics: The use of telematics systems to receive fault codes and alerts can lead to the ability to fix issues before they become more time consuming and costly to repair. Today, shops can use those technologies for insights and real-time data.
During an Endeavor Commercial Vehicle Technology (CV Tech) educational event, a panel of industry experts shared insights on how telematics is helping to improve maintenance practices and optimize uptime. As reported, the group also discussed how the path to a predictive maintenance model starts with implementing and adhering to a comprehensive PM program.
You need to walk before you can run, said Brian Mulshine, Director of Aftermarket Customer Experience for Navistar. He suggested all PMs be up-to-date and fleets be sure to address any fault codes on the vehicle.
“First, you have to do your maintenance. Second, you have to fix fault codes,” he stressed. “Then we can start talking about predictive maintenance and start getting really proactive.”
“The evolution of maintenance starts at the PM,” added Gerry Mead, Executive Vice President of Maintenance and Equipment for Hub Group. “And if you’re not doing the PM, it doesn’t matter what you do, you’re going to fail anyway; you’re never going to get to predictive [maintenance].”
Integration of vehicle information into the shop diagnostic tool is key to ensure streamlined service from a roadside event as that vehicle makes its way into a shop, said Scott Bolt, Vice President of Product Management for Noregon. “Having that history and that information all rolled up into one makes a real, big difference when it comes time to repair the vehicle,” he added.
“When you integrate these shop systems on the floor, what you end up doing is you’re able to more efficiently schedule your vehicles to come in and be [serviced]; you can coordinate when the parts are going to be there, and when the vehicles are going to be there, and when the technician [whom] is able to do the work is going to be there,” Bolt said.
Having a clear understanding of the causes of vehicle downtime is a great place to start
More often than not, service providers say that parts availability issues can slow down service work, something that can be addressed easily by maintaining an inventory of regularly used items.
“We count on our vendors to supply the parts we need,” said Irvin Bowman, President of Wayne Truck & Trailer Ltd. “We work hard to have those relationships with a variety of suppliers, including dealers, wholesalers, and aftermarket parts providers.”
It might also be surprising to learn that a large part of unscheduled downtime can be traced to inefficient management processes and a lack of communication.
Communication is key to reducing downtime, noted Troy Willich, CEO/Co-Founder of TDI Fleet Services. “Sometimes it’s just a matter of getting a customer’s approval to go ahead with a repair but technology makes that easier today,” he said. “Still, it requires a smooth process to avoid bottlenecks.”
Fleet maintenance software has capabilities that help reduce downtime and costs
Regardless of the cause, what heavy-duty repair services providers and their customers often find effective for reducing unscheduled downtime are integrated shop management systems. Companies that are taking advantage of their maintenance software are finding it easier to improve uptime.
With those systems they can avoid unnecessary downtime by more effectively managing inspections, PM programs, and shop operations.
They can address customer communication issues by using the software to plan and track the servicing and repair of vehicles, and to alert customers when PMs are due, about estimates, and when vehicles are ready to return to service.
The software can reduce administrative tasks by automating parts purchasing from designated vendors, helping to streamline processes and speed up repair times.
With data analytics and reporting capabilities, shops can use software to identify the reasons behind unscheduled events and avoid recurring issues by addressing them proactively.
While some factors behind downtime are beyond anyone’s control, the cost of unscheduled service events adds up quickly for your customers. With the right approach, however, you can keep your customers’ vehicles and their drivers moving and drive up their satisfaction with your services.