The Ghost of Obsolete Parts Past
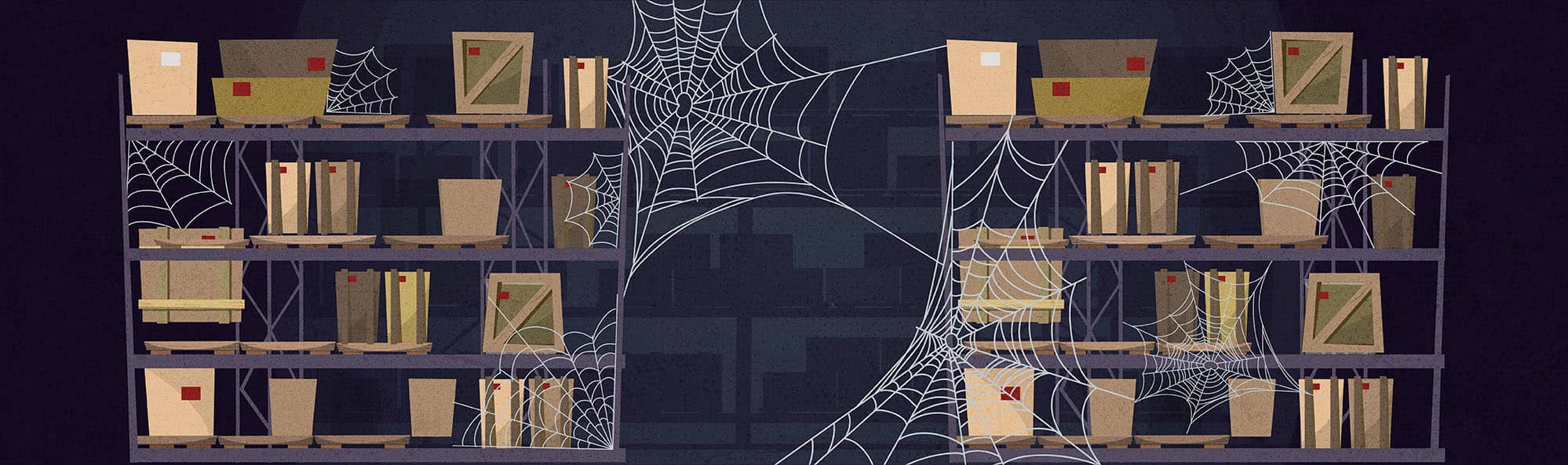
Gather around, friends, for today we address a topic we cannot claim is near and dear to our hearts. It is a subject spoken of in hushed tones, a horror that drifts through our industry and almost every other one in some form.
It is the malevolent ghost haunting your parts room, turning all it touches into rust (or at least unusable junk). It is a strange boon for online sales platforms like eBay and others.
What is this fearsome thing?
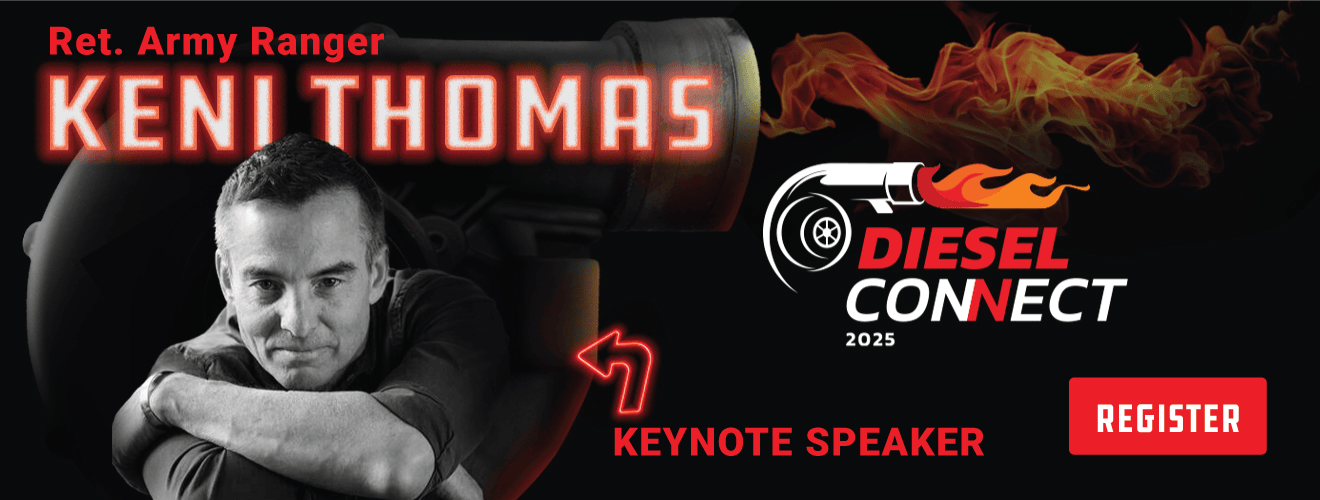
Parts obsolescence.
Yes, friends, we are talking about that terrible time in everyone’s life when the parts you have are just no longer usable in repairs. Usually this occurs because they’re no longer produced by the manufacturer.
But hey…maybe parts obsolescence doesn’t have to be scary. Let’s look into it further and see what some shops are doing to deal with it.
WHAT LEADS TO PARTS OBSOLESCENCE?
Sorry bud. Any shop that carries a decent amount of inventory will eventually face the horror of obsolete parts. In many cases, this is just part of the natural cycle of life.
(Editor’s Note: Don’t you mean, “IT’S THE CIRCLEEEEE OF LIFE,” Suz?)
…fine, I’ll allow it.
Anyway, we see it in our industry as new trucks are being manufactured with new components. This does not mean the old trucks immediately stop working, but manufacturers may stop making the components those older trucks need to run. Then those trucks are phased out for lack of parts, and, well…if you’ve got any of those parts left, you’re probably wondering if you’re in some trouble.
In some cases, says Ashley Sowell of Integrity Fleet Services in Texas, these manufacturing changes and stoppages are due to labor shortages all over the world, including in the manufacturing area (ooooh, we know plenty about that, don’t we?).
“Obviously, production times are gonna be lower if these items are being manufactured—if there’s not people to make the production happen, or happen fast enough,” she says. “Then you’re going to have back orders, and then they start to evaluate what’s really important: these 10-year-old items, or these new ones we can sell X amount, vs. [the older parts], which may be a one-off.”
I HAVE OBSOLETE PARTS…WHAT DO I DO?
First, don’t panic.
Pour yourself a cup of coffee. The parts aren’t going anywhere unless you decide to do something with them, so you’ve got time to chill out and watch some Netflix (or read this blog) before deciding what to do.
Not all obsolete parts immediately need to be binned. If they are in good shape and you’re still servicing vehicles that require them, well, you can use them. The trouble most shops see, though, is when demand for obsolete parts just disappears, and suddenly they’re left with stuff just sitting there.
“If it’s something we know we can move, we’ll keep it,” Ashley says. “But if not, we take other avenues.”
Those avenues include manufacturers or vendors that will buy back what you can’t use. You may also look into eBay, Amazon, Craigslist, and other online platforms to list obsolete parts.
You may at some point be confronted by the parts you can’t unload in some way. These may end up at the scrapyard or donated or used for personal projects.
When asked what sort of components she saw falling into obsolescence over time, Ashley reports that the really old equipment seems to fare the worst. “Some of the mechanical parts are more difficult to find,” she says, “because a lot of newer units can be replaced with computer parts that would serve the same purposes.”
HOW CAN I KEEP OBSOLETE PARTS OUT OF MY INVENTORY?
“We use Fullbay for that,” Ashley says.
Wait, a shameless plug that isn’t from us?
Yup. We went there.
Integrity Fleet Services tries not to stock uncommon parts. “There’s just too many varieties of equipment, engines, etc.,” Ashley says. “Unless you’re a parts dealer, you cannot feasibly stock all those parts.”
And yes, Fullbay can help you out with that. Mario Cortez, Parts Manager at Donahue Truck Centers in California, uses Fullbay to categorize obsolescence in Fullbay to measure their movement. Here’s how:
Add OEM and aftermarket cross-reference to see as many parts as you can.
A parts cross-reference like the one from MOTOR helps you track down aftermarket parts to help you complete a repair. Neat, right?
A solid parts cross-reference can help you out if the opposite occurs, too. If you have a part that you think might be obsolete, check a parts cross-reference to see if there is a surprising truck or vehicle that you can still use that part on.
(Yes, you can get MOTOR’s parts cross-reference through Fullbay!)
Try to send items back to the vendor—take a hit on the restocking fee.
What’s better? Taking a 10-15% restocking fee hit or having that part and its brethren sitting on the shelves for years and years, gathering dust until they are tossed into a garbage bin or fall apart, only to haunt your shop as The Ghost of Obsolete Parts?
Yeah. The restocking fee isn’t too bad, especially if you remember that a) You’re opening shelf space for parts you’ll actually move, and b) When you get your inventory in order, you won’t have as many parts that need to go back at all!
Closely monitor “We need to stock these” feelings.
Basing your parts ordering around gut instinct will end up costing you time, space, and money. Probably a lot of money. Basing your parts around someone else’s gut instinct will do the same.
Most parts managers have probably had those days where techs have said, “Jumpin’ junebugs! We need to stock 30 zerks!” No matter how excited the techs are about those zerks, though, hold back. Look at your buying history and the reports. What if you only use five zerks a year? Stocking up on 30 means you’ll have 25 of them just sitting in the parts room…gathering dust…going obsolete…
You get the idea. Take into account what techs and other departments are asking for, but do your own research before buying a bunch of stuff.
Create return locations for any non-stock parts that need to be sent back.
If you do have unused parts that need to go back to a vendor, make a place for them and make sure everyone puts them there. It can be a dedicated bin, a shelf, whatever. Otherwise, parts might get stashed back in the parts room, or in a crawlspace, or behind the coffeemaker, and who needs that?
But Mario didn’t stop there! He also added the following suggestions:
- As a parts manager, know what obsolescence you have in your inventory.
- Organize your inventory by category and manufacturer.
- Walk your inventory to see if there is anything out of place.
- Closely monitor your general bin.
- Closely monitor parts orders from the team.
- Closely monitor the service department’s parts returns.
FULLBAY CAN HELP
Yeah, yeah, another Fullbay plug. Hey, we already featured praise from Ashley and Mario—so let’s make it an even three and call it a day.
Fullbay brings a lot to your repair operation, including your inventory. Maybe especially your inventory. Customizable reports make it easy to see exactly what’s moving and what isn’t, allowing your parts manager (or you!) to make buying decisions backed by data instead of just gut instinct. And when you’re making the right choices about parts, you’ll have fewer obsolete ones sitting around…whispering to each other in the dark…climbing down from their shelves, leaving trails of rust or flaking chrome behind them…
(Editor’s Note: We get it, it’s October, you want to be spooky. Reel it in, Suz. It’s the conclusion.)
Leave the Ghosts of Obsolete Parts Past to Dickens and maybe Netflix. Trust Fullbay’s inventory features to keep your parts room lively and functional.
Ready to thwart some repair room ghosts? Give our free demo a try!