Too Many Cooks In The Parts Kitchen
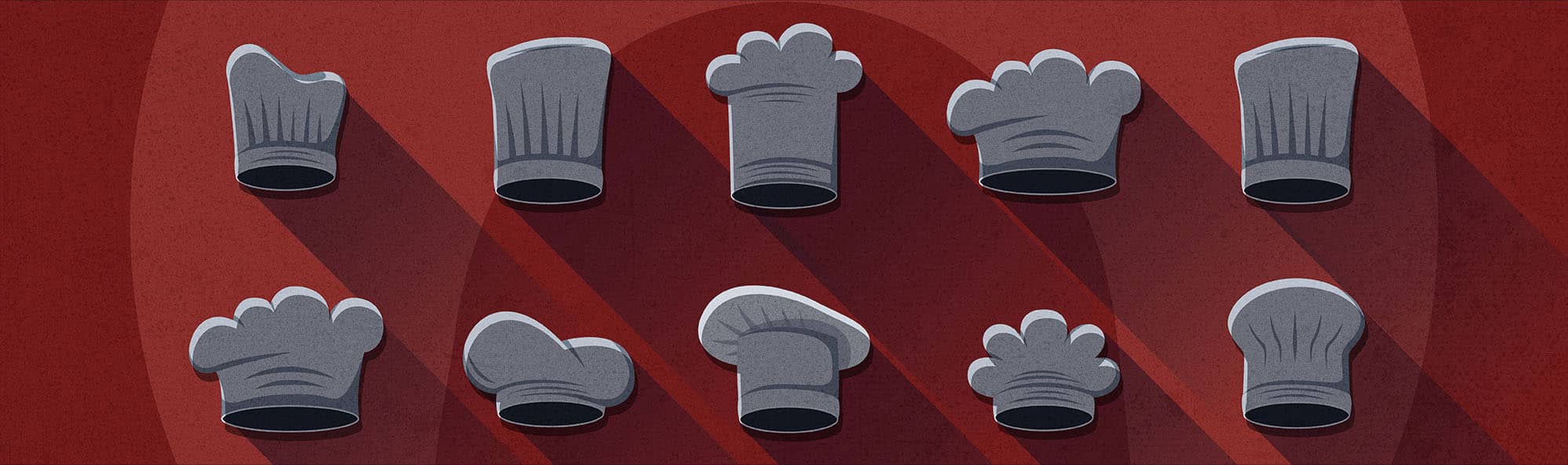
In an ideal world, your parts are exactly where you need them, when you need them.
Alas, we do not live in an ideal world.
You’ve heard the old saying, “Parts is parts,” but really, maybe we should change that to, “Parts have a mind of their own.”
Sometimes they disappear and reappear seemingly on a whim. This can lead to some…er…aggravating situations where Tech A doesn’t have the parts they need because Tech B ran off to fix a truck with them, or a code got changed and now no one can find what they need, or someone dropped coffee on the spreadsheet and, well…
You get the idea.
So, how do you make sure you’re tracking your parts and have a good process in place?
We sat down with Zeb Todd, parts manager at The Service Company, to get his perspective on the flow of parts. He laughed, saying, “I’d love to know how others do it, too.”
Getting parts where they need to be remains a long-standing issue for many a repair shop, both heavy-duty and automotive. “One of my employees came from a very large dealership, and he said they struggled with it there,” Zeb tells us. “They invested a lot of money in inventory control, and they’d scan everything in and everything out…same thing, though. You’d go back to a bin that’s supposed to have three parts in it, and there’s zero. Or 12.”
Zeb graciously talked us through some of the processes and steps The Service Company maintains to keep their parts flowing in a semi-steady fashion. Bear in mind this is how one medium-sized chain is handling the parts conundrum; some of what we talk about here may not work out well for a smaller operation. But we do think there’s some pearls of wisdom in here for anyone to borrow and apply to their own parts issues.
Keep reading—and get into the flow.
WHAT IS “THE FLOW,” THOUGH?
When we say “flow,” we refer to the route parts take to reach the shop, techs, and eventually customers. That flow is going to look a little different for every shop, depending on size, staffing situation, and so on.
The Service Company’s parts flow generally follows four steps. We’ll describe them below, along with some of the problems that can accompany each step:
- Parts arrive. Zeb has a guy who works in physical shipping and receiving. “His accuracy is the start of all this,” he says. Were the right number of parts ordered? Did the right number of parts arrive? Is it a special order for a truck or for inventory, or a store transfer from another branch?
- Electronic entry. Someone is taking the physical information and putting it into the computer, and that can mess things up—clerical errors like typos can abound if you’re not careful.
- Putting parts away. The next step in the parts flow is actually introducing the parts to their new home, whether that’s inventory shelves, shop will call, or delivery shelf to be dropped off at a customer’s location.
- Cycle counting. “There’s always an opportunity for someone to miscount,” Zeb says. “Or maybe no one miscounted, but the part wasn’t put away correctly, or you have bad bins.”
There’s a lot of people involved in each process described above. And with all those cooks in the kitchen, so to speak, how does a repair shop keep its inventory and special order parts accurate?
KEEPING THE RIVER MOVING
The first step toward really managing the parts flow is ensuring accuracy when documenting parts as they come in.
At The Service Company, the person in the back handling the receiving starts by reviewing all parts as they come in. If there’s a discrepancy like damaged packaging or an overage, he’ll take note of it.
The next person in line will review the received notes and data, double-checking everything once more while making an electronic record of it.
Zeb stresses the importance of electronic records. “Paper has a tendency to disappear, get stepped on, have coffee spilled on it, or just get shredded…or it falls behind a filing cabinet,” he says. “The person doing the electronic receiving is getting notifications all day long as the person doing the physical receiving is submitting purchase orders as completed.”
When the person handling electronic receiving reviews each file, they can see the notations on them, and can contact the vendor if necessary to account for overages, damaged parts, or other issues.
The next potential kink in the hose is figuring out who pulls the parts.
A lot of shops have techs pull their own parts. Sometimes there’s no help for it; you need a part, you don’t have a runner (or your runner is elsewhere), your parts manager is in the bathroom—whatever. It happens. But the more you can keep your parts with your parts people, the more organized things will be.
CLEAN PARTS ROOM + CYCLE COUNTING = FLOW LIKE WATER
Speaking of organization, Zeb attributes a lot of his shop’s flow to how they manage inventory overall. Don’t underestimate the power of well-organized shelves and a thoughtfully laid out parts room. “All of that is key to keeping the flow going,” Zeb says. “I like cycle counts a lot more than physical inventory, personally. If you have a cycle count—every person has a section they’re responsible for every month—and part of cycle counting, to me, is bin maintenance, reorganization, room issues, and the accuracy of the count.”
Compare that to doing physical inventory once or maybe even a few times a year, where your crew is so pressed to get through the task in a few days that they tend to bypass issues like shoddy bins.
With a cycle count, you’ve got a whole month. If you have 500 part numbers you need to count, you do that, but you’re also responsible for bin maintenance and everything else on that shelf.
“I feel we’ve gotten more successful at the flow of parts being accurate and moving in and out,” Zeb says. “It gives you time to actually sort things out.”
Another important component of parts flow is the will call. “Equipment in your will call, whether it’s for the counter or the delivery shelf…it’s key to keeping the shop moving. Let’s get the parts in our will call current. Let’s get it billed out.”
REMEMBER, NOBODY’S PERFECT
Running inventory smoothly can feel a little like playing whack-a-mole. You stamp down one problem, but another pops up.
“I think every shop struggles with it,” Zeb says. “If they don’t, they’re either unusually perfect or they don’t have many parts running through their shop. Everyone I’ve ever talked to struggles with this issue.”
The bottom line is this: Getting the right processes in place can help you manage the flow of parts and ensure everything is generally where it should be. Problems will still crop up, but maintaining a system of checks and balances will help keep your parts where they belong and your inventory in order.
While Zeb’s processes may not be a perfect fit for your shop, we hope he’s offered up some great ideas that you can use to build out your own personalized flow of parts—one that perfectly fits your shop’s needs.