Oil Condition Monitoring for Heavy Duty Machinery
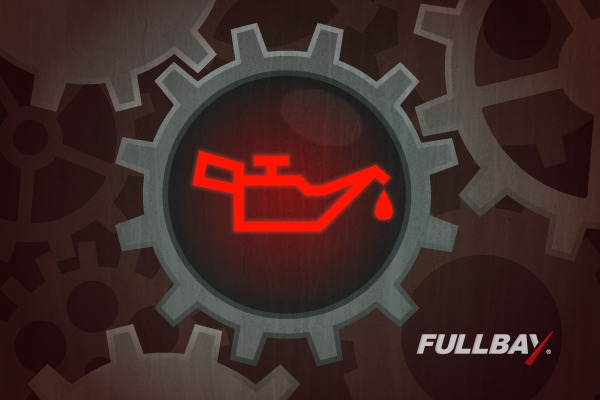
Even those fleets that have leveled up on the maintenance maturity scale can always improve their maintenance game. Oil condition monitoring (OCM) is one way to do that. Keeping an eye on the condition of a semi’s oil makes you more aware of how the truck is performing. Since knowledge is power, you’ll also be in a better position to schedule maintenance and control downtime. Oil condition monitoring is a small extra step that could result in big savings—of both time and money.
Why Oil Condition is Important
Fuel may power your heavy duty truck, but oil is its lifeblood. It keeps the engine’s moving parts lubricated, affecting the vehicle’s efficiency and performance. Oil condition monitoring is essential because oil degrades with use over time. Dirt and particles start contaminating it, causing oil to become sludgy and lose its lubricating effectiveness. Sludgy oil is also less effective at dispelling heat. That means engines running on dirty oil have to work harder. The bottom line is that oil condition is a serious matter. It’s a safety issue that not only reduces the life of the engine, but it also cuts fuel efficiency.
Benefits of Oil Condition Monitoring
Scheduled oil changes are supposed to ensure your trucks have clean oil on a regular basis. However, monitoring oil condition takes that preventive step up a notch. Not all trucks necessarily need an oil change every “X” number of miles. Some fleets schedule oil changes based on hours driven, but that’s not really a one-size-fits-all solution, either. Oil condition monitoring is the only way to know that you’re not replacing oil that doesn’t need changing. Plus, it ensures that trucks that need a change are getting them soon enough.
That puts a whole new spin on mastering downtime. Instead of resigning your fleet to working around a certain number of trucks being out of commission when PM time rolls around, you can schedule oil changes for only those trucks that really need it. What’s more, besides safely extending the intervals between oil changes and giving you more control over downtime, there are additional benefits to OCM done right. It can also extend warranties and cut maintenance costs—and that results in increased profits.
Applications for OCM
Since practically all mechanical equipment needs some type of lubrication for optimal performance, oil condition monitoring is widely used in industrial applications such as:
- HVAC and building maintenance
- manufacturing
- utilities and power generation
- waste treatment
Agriculture and forestry as well as construction and mining all use OCM. Naturally, because heavy duty trucks work hard and need to perform optimally, fleet owners and managers are realizing that oil condition monitoring is vital for increasing profitability and ROI.
Ways to Implement OCM
Oil condition monitoring isn’t as simple as checking the residue on the dipstick. It’s a more precise process, and it needs to happen frequently. Some fleets practice OCM monthly while others do it quarterly. There are two preferred methods for getting the job done:
Testing and Analysis
Providing a sample of your engine oil to a lab for analysis is one of the common ways for fleets to monitor oil condition. Samples are acquired from the engine by drawing it out with a vacuum pump or opening the oil drain plug and letting enough flow out to fill the sample bottle. Then, you mail or send them via delivery service like UPS or FedEx to the lab of your choice. There, testing and inspection take place. Labs that specialize in OCM are scattered throughout the U.S., so the testing and analysis process can take at least a couple of days. Most labs promise a 24-hour turn around once they’ve received your sample. They can call you with the results ASAP. However, they’ll also provide detailed written reports for you to keep on file.
Oil Quality Sensors
For an alternative to the testing process, you can get oil quality sensors (OQSs) that let you perform your own oil condition monitoring in real-time without having to be a chemist. That saves the trouble of collecting samples and mailing them out. Current technology has allowed the creation of ultra-sensitive devices with high accuracy. The sensors tell you the quality of your trucks’ oil now. That beats finding out about it 2 or 3 days down the road.
OQSs sound high-tech, and they are, but adding an oil quality display (OQD) simplifies the process as much as possible. OQDs show you the temperature and condition of the oil as the OQS reads it. That means no hooking up to a computer or installing another piece of software. Just make sure to connect the OQD, then record the reading on the display.
OCM and Scheduling Maintenance
If you’ve discovered the value in predictive maintenance, you probably already see how useful oil condition monitoring can be. Routine readings give you the data you need to schedule maintenance more effectively on a predictive level. Maintenance can happen just-in-time while still staying ahead of breakdowns and repairs, and that makes for super-efficient fleets.
When implementing OCM, you can start with your next scheduled PM. Whether you take your trucks to a shop or have an on-site or mobile tech, have them take samples when they drop the oil. A visual inspection will likely confirm that most of the trucks probably do need an oil change. However, there may be oil from one or two that doesn’t look too bad. You can still go through with the planned maintenance but have those questionable samples analyzed and log the results. Then, continue with oil condition monitoring monthly, quarterly, or on the schedule that best fits your fleet.
Fullbay is the perfect place to keep track of OCM data. Much like a medical history for humans, Fullbay tracks your fleet’s history, truck by truck. At the click of a button, you’ll have access to information like when maintenance was performed, what repairs were done, and what parts and products were used. It’s the one place to find all the important data on all your trucks, and the logical spot for keeping oil condition results. Fill in the form below to see how Fullbay can help manage oil condition monitoring to make your fleet safer, more efficient, and more profitable.