Lightweighting Heavy-Duty Trucks
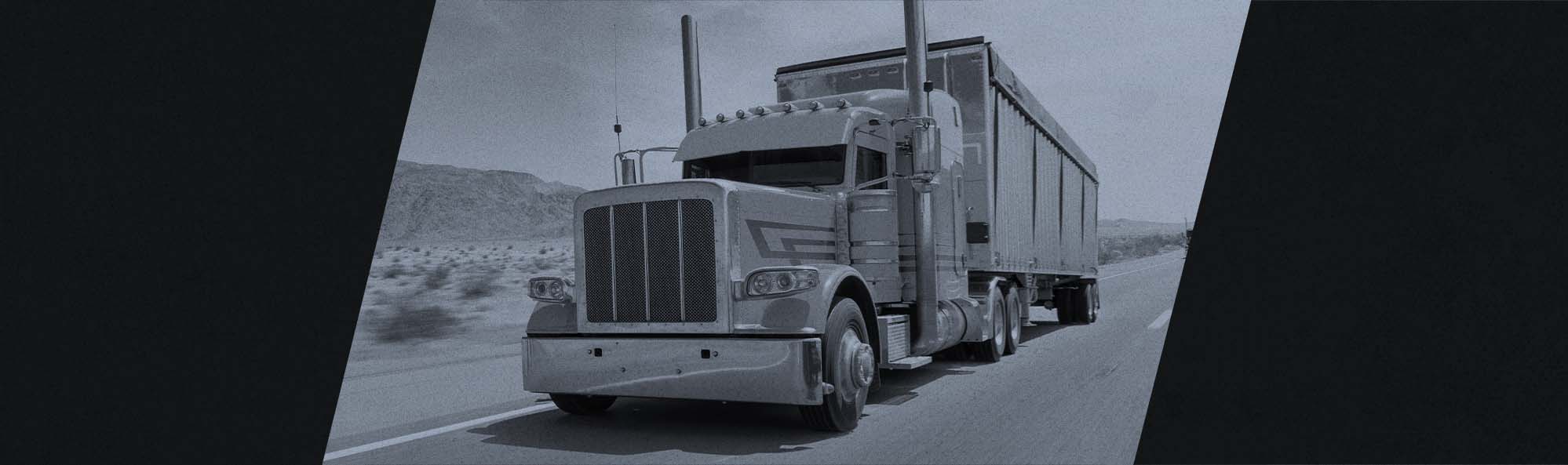
Federal weight limits on semis have been in place since the mid-1950s. The purpose of the guidelines is to enhance safety as well as maintain interstate roadways. While those are important matters, the freight industry has struggled with limits and looked for other options for as long as anyone in the business can remember. The issue has become more pressing as the demand for faster delivery and less expensive products rises. In 2010, the government teamed up with truck builders to improve fuel efficiency with lightweighting, smoother designs, and other features.
First, a Look at the Limits
Basically, federal rules say a Class 8 truck cannot weigh more than 80,000. Fleets and owner/operator businesses pay tax based on how many pounds they carry. Some of the money goes toward road maintenance. Though there are some exceptions to the limits, it applies to total weight. That’s including the truck, trailer, fuel, driver, and the cargo. That means taking away a lot of weight from 80,000 pounds to figure out how much cargo a truck can haul. Of course, that affects the bottom line.
Lightweighting Improves Fuel Efficiency
Lightweighting is the practice of building a truck out of lightweight materials to make the vehicle lighter in general. The government program we talked about earlier, known as SuperTruck, not only focuses on lightweighting semis but also on creating lighter trailers, too. By using aluminum, high-strength steel, and a mix of lighter-weight parts, the goal is to improve fuel efficiency. Lighter trucks and trailers don’t use as much fuel. They can pick up speed faster and stop shorter, too. That means better gas mileage, and that’s just one of the benefits of lightweighting.
Carry More With a Lighter Truck
Cutting fuel costs is one valuable benefit of lightweighting for fleets, but increasing payload potential is another biggie. Every pound you take away from the truck and trailer is another pound you can haul. That’s good news for most fleets, but fantastic news for weight-sensitive carriers that haul fuel, liquids like drinks, and other bulk products.
Does Lightweighting Affect Maintenance and Repair?
Though manufacturers such as Peterbilt who already practice lightweighting say that no special maintenance is needed, repairs are a different story. It’s true that aluminum resists rust, but it costs more to fix. What’s more, repairing aluminum components involves specialized tools, equipment, and even training. Shops should also have a separate work area for aluminum repairs to eliminate the risk of cross-contaminating with other materials.
Shops that specialize in lightweighted trucks won’t have any problem keeping track of service and repairs with Fullbay software. Fullbay builds a history on each and every vehicle. It creates a “medical record” of sorts for every heavy-duty truck that comes through your shop. It makes it easy to find out what’s been done and which lightweight parts have been repaired or replaced. Plus, with Fullbay you can track parts inventory, make orders, and create estimates and invoices. When it comes to keeping up with the industry, you’ll actually be a step ahead with Fullbay.