Inventory Cycle Counts
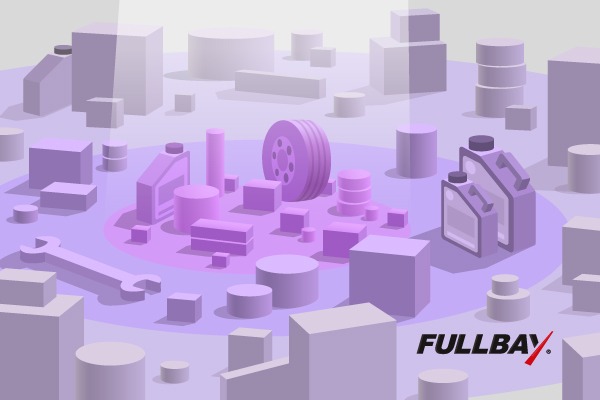
Inventory is a vital part of any heavy-duty repair shop. Whether you’re an owner operated shop or one under a fleet or inside a dealership, you have stock. You need parts on hand to perform maintenance and repairs. However, inventory can quickly get out of hand if you don’t keep an eye on it. That’s the catch. Very few people enjoy counting and tracking parts. Unfortunately, un-managed stock tends to turn into a gaping hole that drains profits. If you love doing inventory as much as having a root canal, there’s a solution. Performing inventory cycle counts will get your stock-on-hand back under control and keep it there.
Inventory Cycle Counts are as Easy as A-B-C
The thought of physically counting all the parts in your stock room is overwhelming. Inventory cycle counts breaks the job down into smaller, more manageable tasks. First, divide the parts you stock into groups and schedule counting them according to how quickly they typically sell. We refer to this system as the A-B-C’s of inventory:
- A’s are fast-moving parts, ones you use frequently like PM supplies, brake shoes, etc.
- B’s are slightly slower-moving parts, ones that sell at a regular rate but not quickly, such as alternators, starters, and the like
- C’s are the slowest-moving parts, ones that sit on the shelf for months at a time like turbos, for instance
Once you have the parts divided into categories, you’ll count them in cycles. Logically, because A’s are the fast-moving parts, you’ll count them most frequently—once a month. As a slower-moving category, you’ll count B’s quarterly and, naturally, count C’s the least frequently, every six months.
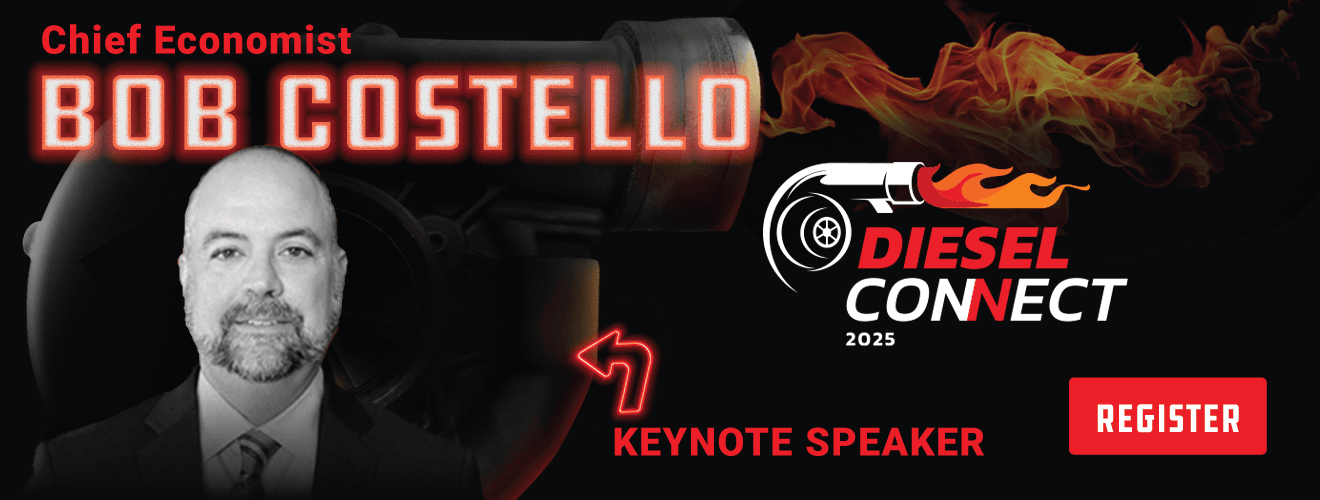
Tackling inventory in this way not only results in more accurate records, but it also keeps the task manageable. Never again will you have to shut down the shop for a day or longer. No more coming in after hours or on the weekend to do the dreaded inventory.
Focus on the Negatives
What is Negative Inventory?
Negative inventory is the one area you need to look at most frequently in inventory cycle counts. You’ll need to reconcile it daily. It happens when the count on your system tells you that there are less than zero of certain parts in stock. Usually, quick-moving parts show up as negative inventory because ordering them, logging them in as received, and using them doesn’t always happen in typical progression. It’s not unusual for an order to get entered into the system as “received” before the parts actually hit the shelves. Also, shops with multiple locations can have problems with negative inventory. It occurs when parts get shipped to one location, but logged in as received at another.
Why is it a Big Deal?
Examining negative inventory on a daily basis as part of inventory cycle counts is essential. Doing it will avoid problems in accounting and for your techs and parts manager. Constantly reconciling them will keep your inventory list accurate so techs know what’s on-hand and managers know what to order. Plus, when it comes to accounting, things like cost of goods sold, job costing reports, vendor reports, profit and loss statements, and balance sheets are among the many bookkeeping items that can be negatively affected by negative inventory.
Tips to Make Inventory Cycle Counts a Breeze
Inventory cycle counts are designed to make managing inventory easier, but there are some tricks to simplifying it even more. For example, store parts in the same category together in the stockroom. Place all the A’s near the front of the room, put the C’s out of the way toward the back, and keep the B’s together somewhere in between.
Next, parts managers are the logical people to be in charge of doing the actual counts. However, it’s helpful to make mobile techs responsible for parts kept on their trucks. Having them do an end-of-week count on the inventory they keep will make the parts manager’s job that much easier.
Finally, enter counts directly into your system on a tablet or smartphone. That saves time and reduces chances of errors created by double-entry. Heavy-duty repair shop management software like Fullbay makes that step possible, as well as making inventory management, in general, a breeze. With Fullbay, orders queue up to go into your inventory list upon receipt. What’s more, parts drop from the list as techs use them. It prints barcodes to help organize your stockroom according to parts categories. Fullbay even builds reports for every category in your cycle count from the A-B-C’s to negative inventory. Experience how inventory cycle counts can make managing parts easy. Fill in the form below to give Fullbay a try.