The Learning Curve, Or How To Train Your Techs Without Losing Tons of Productivity
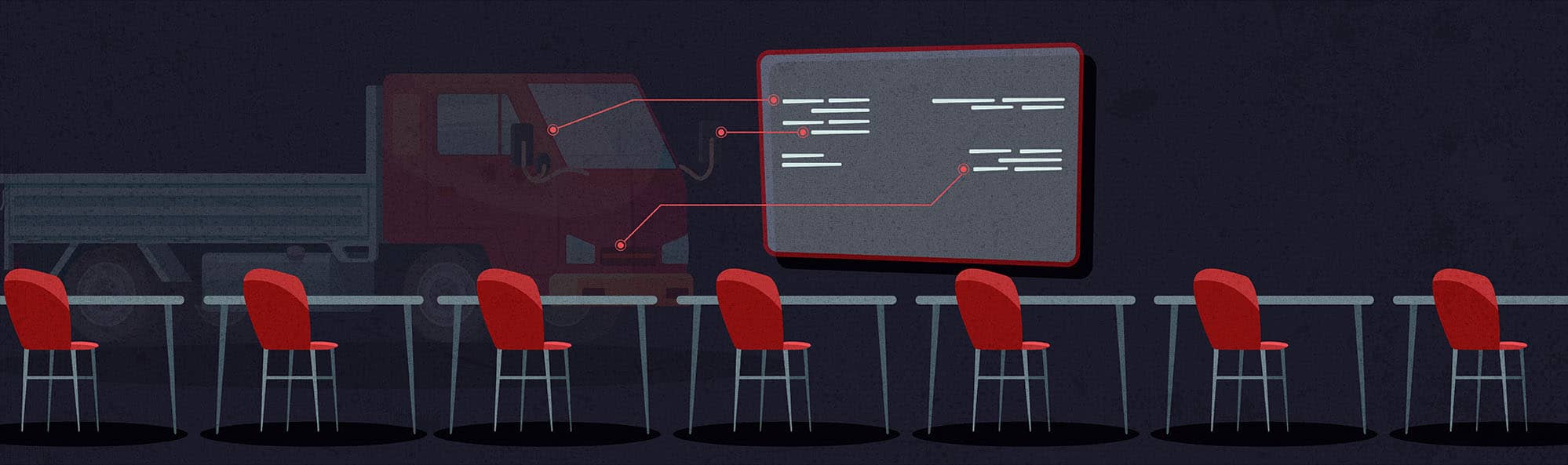
If anyone who keeps learning stays young, then continuous training must be the Fountain of Youth.
Right?
Right?!
(Editor’s Note: Move it along, Suz.)
All right, here’s some more context. At the end of every webinar, we open up the floor (well, the chat component) to questions and suggestions for future topics. One of the themes we see popping up with some frequency is training—namely, how do you get your techs trained when they need to be, and how do you train them without losing a lot of productivity?
We were intrigued, so we reached out to several repair shops to get their take on training:
- Troy Willich from TDI Fleet Services in Texas
- Jimmy Wall from Donahue Truck Centers in California
- Glen Grader and Andrew Pope from Integrity Fleet Services in Washington
We may not need to say this, but we will anyway: When it comes to training, your mileage will vary based on the size of your operation, your location, and what exactly you’re training your techs on. No matter which way you spin it, a larger shop will be more equipped to cover for a tech who’s out for a day or two learning the ropes on a new Peterbilt or something.
But even if you’re running a tiny operation, you will, on occasion, need to train your tech(s) (or yourself!). It often comes down to the following tactics, which we’ll get into below:
- Determine whether your techs need training—is it an urgent update, or optional?
- Set aside time for training (and compensate your techs for it).
- Set aside time for safety-related training, but require techs to pursue further education off the clock.
Let’s get training!
AN IMPORTANT DISTINCTION: APPRENTICESHIPS VS. CONTINUED EDUCATION
We’re going to refer to two separate (but equally important) types of training in this article. The first is an apprenticeship, which you can probably figure out on your own—it involves a new technician learning the ropes. The second is continued training or continued education, where a seasoned technician learns how to diagnose, repair, or otherwise work with a new vehicle model, component, or software.
In general, the shops we spoke to will set aside time for safety and compliance training, but product training will be tackled as needed (and on or off the clock, depending on the operation).
HOW TO TRAIN NEW TECHNICIANS
Donahue and Integrity Fleet Services both look to the old hands to wrangle the young’uns. Most of this comes in the form of on-the-job training, where a newbie might stand next to or across from a seasoned tech and, well, learn by doing.
“We’re not a small shop, but we’re not a huge organization with lots of resources,” Glen says. “We pretty much have to rely on our senior techs … work with someone who knows how to do it, and get guidance.”
It’s not as formal as an apprenticeship, but that’s a pretty close comparison, so we’ll stick with it. It can be a fantastic way to learn—but yes, it’s going to slow things down. Even your fastest, most senior technician is going to see productivity drop as they try to instruct a new person. That’s an accepted part of things.
“It’s gonna take a good while for a guy to get up to speed, and during that time they’re going to drag others down with them as they’re teaching,” Glen adds. And even after the initial hand-holding period is over, a new tech will still need close supervision and have their work checked over before they can officially head out on their own to dazzle the diesel world.
Yes, that’s productivity lost, and time and money spent—but a new tech is an investment. You’re putting this effort into them to help them grow into a valuable and knowledgeable member of the team—these days, good techs are worth their weight in gold.
As an aside, we encourage providing your senior techs with some additional compensation for training, if that’s possible for you. Particularly if your shop runs on a flat rate, they may be seeing less money while educating the next generation. So don’t penalize them for bringing up the newbies!
MINIMIZING LOSS OF PRODUCTIVITY DURING TRAINING
So…let’s be blunt. There is always going to be some kind of slowdown involved with training, whether you’re bringing a new person aboard or sending your techs to an OEM to stay current. You can minimize this loss by performing what the marketing team calls scheduling sorcery.
(Editor’s Note: We don’t call it that.)
Almost every shop has some slow periods. Maybe it’s not quite downtime, but it’s still quieter. “If shops were always busy, we wouldn’t have to measure productivity,” Jimmy points out. At Donahue, the rule is if there aren’t trucks rolling into bays, then techs should be training (er, with the permission of a service manager).
For the most part, techs aren’t heading offsite to do this training, either—most of it is available online and on demand. Rather than sitting around in the bay or milking the clock on an existing job, techs can get in a half-hour of training here, or 15 minutes there. They’re still available to jump on a job if necessary, but if things are quiet, they can work on their skills.
So, take a look at your scheduling: When are your slow times? If, for mysterious reasons, you open the doors at 8 but don’t see trucks roll in until 10, think about encouraging your techs to catch up on training during their second (or third, or tenth) cup of coffee.
Remember, though, all shops handle things in their own way. Troy at TDI takes a slightly different tack: “Generally, we have technicians learn on their time off,” he tells us. “Personal improvement is a responsibility that mostly falls on the individual.”
A WORD ABOUT THE OFFICE
The focus of this article has largely been on techs, but the productivity difficulties associated with training can slow down your office work, too. “Any time you take someone off [their usual role], they’re focusing their energy elsewhere,” says Jimmy. “Office can be a little easier, unless you’re a very small out—then taking someone out for a half-day training means nobody [is on the desk].”
That’s something to keep in mind if you’re adopting, say, a new computer system, new software, or something else that will otherwise throw a wrench (no pun intended) into the workflow.
NEVER STOP LEARNING
There is unfortunately no silver bullet (or magical equation) to determine how much training your techs need, or when they should get it. In general, how often you try to train your techs will depend on your shop’s circumstances, like how large you are, who your primary clientele are, and whether you have relationships with OEMs.
Shops that are or are partnered with dealerships or manufacturers will need to complete a certain amount of training if they want to continue working on those types of vehicles.
Independent shops have some more freedom in this regard, although some opt into OEM training if they can get it. Integrity Fleet Services maintains good relationships with local dealers, and often sends their techs along for updated training. “I’m sure it’s not everything [the dealer techs] are learning,” Andrew says, “but it’s enough for our guys to get going on things.”
Everyone we talked to agreed on one point: Training is important for everyone.
“I think when we stop learning, we stop growing,” Jimmy says. “We become stagnant.”
Stagnation is terrible for water, for the industry, and for life in general. So keep on learning—even if you don’t hit the Fountain of Youth, you’ve surely found the next best thing.