Making the Heavy Duty Service Manager’s Job Easier
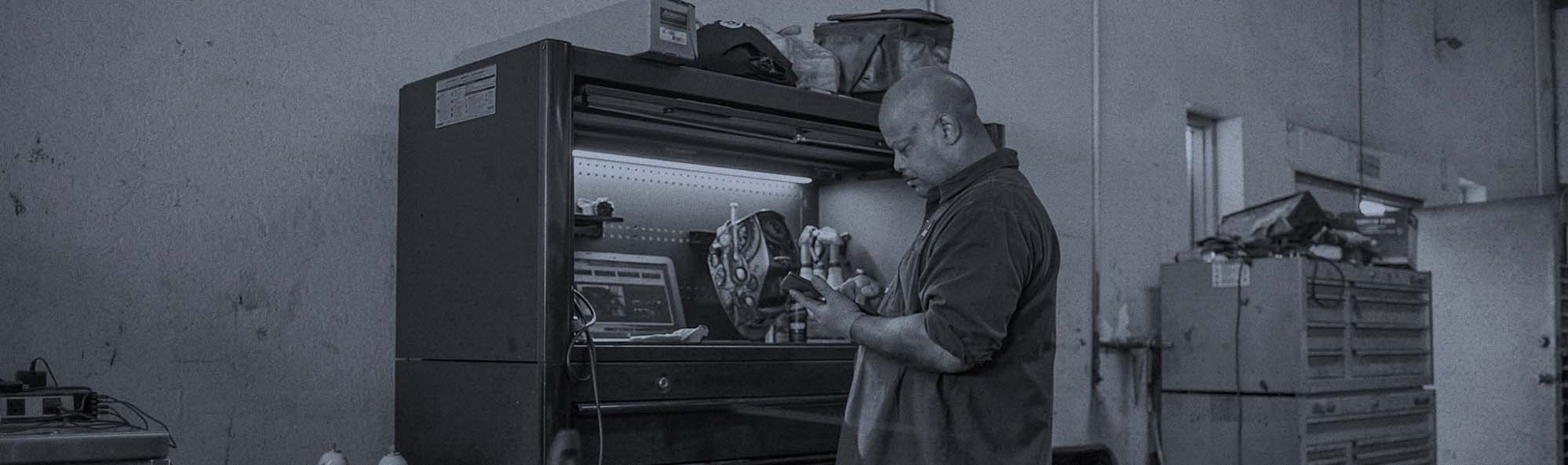
Much of a shop’s success sits squarely on the service manager’s shoulders. With duties that include scheduling work, assigning the right tech for each job, and communicating with customers before, during, and after repairs, the service manager’s job is arguably the toughest one in the shop. He’s like the quarterback of the shop. That’s where fleet repair software comes in. The right program helps with all aspects of the heavy duty service manager job, making it much easier.
Scheduling Work With Fleet Repair Software
Maybe you have a large customer base constantly calling and needing work. Or maybe your shop is still in the growing process. That means having to juggle the increasing work coming in as the business’s reputation builds. Either way, scheduling repairs is a time-consuming balancing act. It requires the heavy duty service manager knowing what customers need and where those jobs fit with openings in the techs’ schedules.
Fleet repair software puts everyone’s schedule in front of the heavy duty service manager at a glance. This helps increase the throughput of the shop, a high priority for all managers. Customers can drop off their trucks and know when they’ll be worked on, and plan accordingly. That alleviates downtime for them and keeps techs busy throughout the day. Everyone would rather have consistent workflow instead of hours of idle time followed by a stress-filled afternoon of trying to cram too many jobs in before closing time.
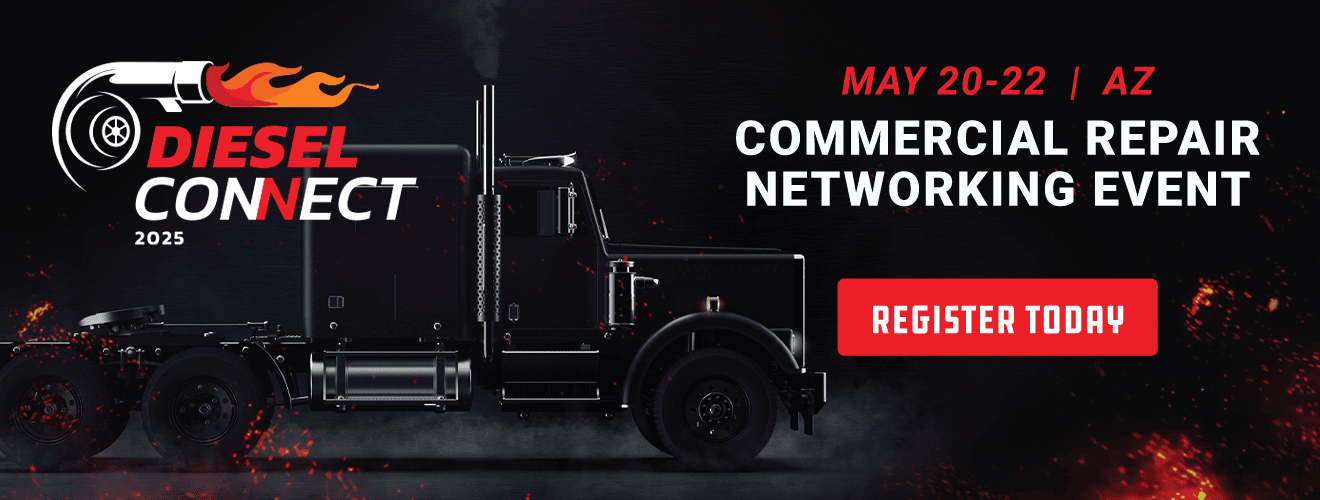
Assigning the Right Tech for the Job
Heavy duty service repair managers know that picking the wrong tech for the job costs money. Some techs do certain jobs more efficiently, so they take less time to perform specific repairs. That opens the door for the tech to bill more hours in a day and the customer gets their truck back sooner. In other cases, picking the right tech eliminates a possible comeback.
Handling both scenarios properly pushes your profit margin higher and improves customer satisfaction, and it’s all possible with fleet repair software. Just as software keeps the shop schedule at the ready, it also shows which techs are available and when. That way, managers assign the right tech for each job, ensuring quick turnaround, optimal repairs, and happy customers.
Helping the Heavy Duty Service Manager Keep Customers in the Loop
Let’s face it: managing fleet accounts and keeping customers happy directly affects whether you get all their heavy duty repair work or just part of it. Developing a great working relationship takes time. It takes trust, and the more your customers trust you, the more work your shop gets. There’s nothing more frustrating than finding out that work was sent to the dealer or the shop just down the road when your shop could have taken on the job. As a shop owner, you know that the more you work on a truck, the better you can service it in the future. Like a jealous girlfriend, you don’t want anyone else touching those trucks. And you won’t wonder what was previously done on the vehicle and whether it was done right.
Effective fleet repair software takes all of that into account. The program not only acts as a “medical record” for trucks, keeping the service history on electronic file for easy review. Plus, it also keeps the customer in the loop. With a portal available to customers on their mobile devices, they can submit service requests, see their fleet’s history, check on repair progress, approve work, and pay you. That keeps the customer in the loop and gives them access to information. It’s an element of transparency that builds trust and deepens loyalty.
The best part about heavy duty repair software isn’t that it makes the heavy duty service repair manager’s job easier. It’s that it does that on top of doing so much more. The right program optimizes scheduling, work assignments, and customer relations, but it also helps with invoicing, ordering parts, and bookkeeping. In short, heavy duty repair software takes your shop’s efficiency to levels you’ve only dreamed of.