Beyond the Semi: An Introduction to the World of Trailer Repair
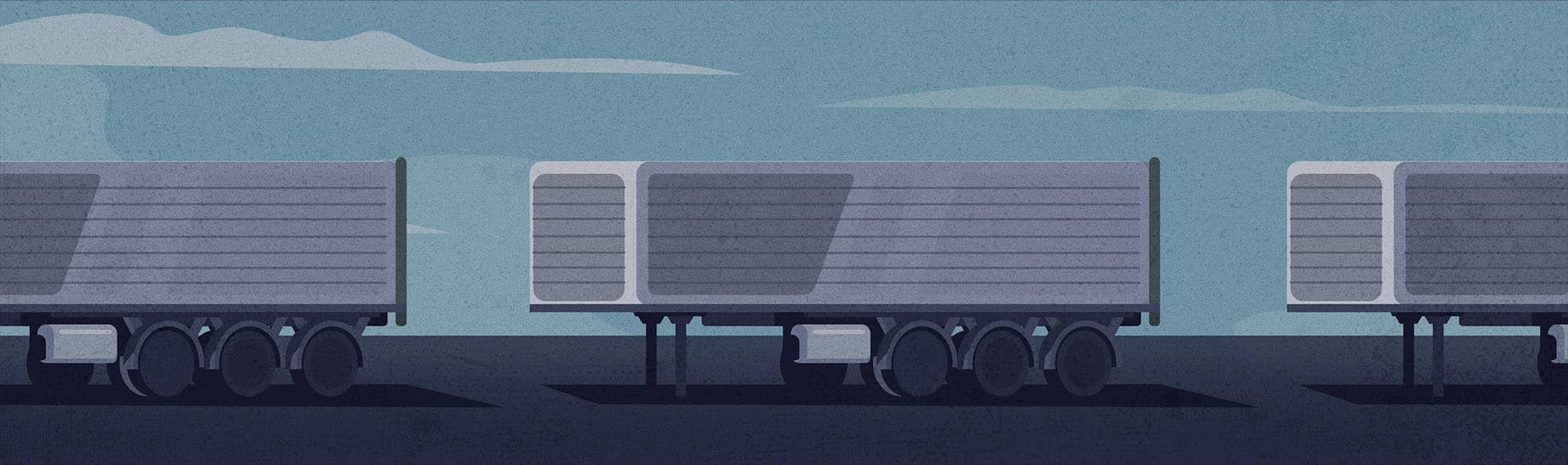
The commercial diesel repair world is vast.
We talk a lot about truck repair because, well, it’s a big part of that vast world—but there’s also a lot more out there. We’ve made it our mission to explore the depths of the diesel industry, starting with our foray into heavy equipment and continuing today with trailers.
Now, those of you in the know might be rolling your eyes. Duh, Fullbay, you’re saying.
But hold up a second. We have it on good authority that people not in the know may well think of tractors and trailers as the same thing. “Truck repair,” in their eyes, isn’t just the semi—it also includes the trailer.
Except, y’know, that’s usually physically impossible because trailers are like a zillion feet long.
(OK, so the federal guidelines cap them at 65, and the trailers Integrity works on tend to be 53 feet. They only seem a zillion feet when you’re trying to pass them on the freeway…I might be projecting.)
Here’s the thing. Trailers are really, really important. All that stuff of ours that gets hauled across the country? It’s in trailers. A truck or tractor without a trailer is just a semi—you can only fit a few Amazon boxes in there. The tractor is the motor, but the trailer is…well…the stuff.
And man, trailers take a beating. They need repairs—often exacting, delicate repairs—and the type of work can be very different from the mechanical world of the diesel engine.
We knew we needed some guidance in this brave new world, so we turned to Glen Grader and Andrew Pope, President and Vice President, respectively, of Integrity Fleet Services up in Pacific, Washington. They got their start at GE Trailer Fleet Services (yes, that GE), leasing and renting trailers, as well as performing maintenance on them. When GE got out of the business, Integrity began.
Since 2011, their operation has repaired both trailers and trucks, though their passion is definitely trailers. They’ve got a huge facility and the expertise to get the job done right, as well as a mobile arm.
So, without further pause, let’s get trailering!
THE BUMPER CARS OF THE HIGHWAY
There are some similarities between trucks and trailers: namely the suspension, brakes, and air system. What most people (including this writer) don’t think about in terms of trailers is the body damage that occurs to them.
“Trailers are kind of the bumper cars of the transportation industry,” Andrew says. In gaming terms, they take a lot of damage. Drivers back into them. Side panels are torn up. Forklift drivers sometimes punch holes in the roofs. Trailers might be knocked over on their sides and slide down the highway.
A SEPARATE SKILL SET
So, trailer repair is closer to bodywork than the mechanical stuff we usually write about. Got it. Glen likens it to carpentry, except trailer techs are plying their craft on aluminum and steel instead of wood.
“There’s a lot of making sure things are squared up and right, and you’re getting panels put back in place, rails are level and straight, and the frame isn’t tweaked. Measure twice, cut once.”
It’s delicate, time-consuming work, often learned on the job.
We know the industry has a technician shortage. Multiply that by like, a zillion for trailers.
Neither Glen nor Andrew could think of any technical school that specifically offers trailer repair. Things like electrical systems and suspension do cross over pretty regularly from the truck side, but the bodywork is an entirely separate skill set. Roofs, ceilings, panels, and so on continually wear out and need maintenance or repair.
Now, up until recently there was a pretty big gap between diesel tech and trailer tech salaries. “That gap has closed,” Glen tells us, largely because “it’s a skill set that is getting tougher and tougher to find.”
He shared some numbers with us: The average fleet is probably running 3 or 4 to 1 power units to trailers. There are a lot more trailers. They’re constantly being damaged on yards, and they’re like an interchangeable piece that nobody thinks a whole lot about until they need it.
Which is of course is all the time.
THE INTERMODAL WORLD
Being located on the coast, Integrity quickly learned about intermodal.
For those who do not routinely think about trailers, here’s a refresher: intermodal refers to when ports take containers off ships and put them onto a bare chassis, essentially making a trailer. But it came in two pieces instead of one.
Integrity handles a lot of intermodal work. “Any repair shop on the coast probably has some level of involvement with the intermodal world,” Glen says. “There’s not a lot of crossover when it comes to the parts and so forth when it comes to a chassis and a standard, 53-foot dry van.”
Think about all the containers that come off ships each day.
(Per the CPB, 11 million containers arrive in our ports every year. Divide that by 365 and you get over 30,000 containers a day being offloaded. Probably not the exact number, but it should give you an idea. I am now done doing math for the rest of the year.)
Those containers and the chassis need repairs, too.
“They’re all steel,” Andrew says, “so it’s all metalwork…fabricating and welding, which is a whole different craft. Our guys can rebuild a bolster on a front chassis and make it look like it’s factory.”
(For the uninitiated, that means Integrity can rebuild the part of the chassis where the containers lock in. This is a section of the chassis that gets torn up all the time and often needs rebuilding. Integrity’s guys can make it look brand new.)
THE REPAIR PROCESS
So, how does a trailer repair specialist like Integrity get work?
Turns out, the same way other commercial repair shops do.
Integrity has both a brick-and-mortar facility and a mobile department. The mobile work tends to be dedicated regular work they do for customers on-site, and the mobile techs will often send trailers (and trucks) to the shop for repairs they can’t easily complete on the field. Their mobile techs also often perform DOT inspections on trailers in the ports (Tacoma and Seattle), which frequently turns up more work.
In other cases, customers will call them and say, “I’ve damaged this trailer…I’m bringing it in for an estimate.”
They also are often called out to customer yards to perform estimates.
“That hasn’t happened nearly as much in the last few years, because of the pandemic,” Andrew says. “They just bring them to us. They need them fixed—they don’t have time to get three or four estimates.”
The fact that these customers bring their trailers straight to Integrity speaks highly of the relationships the team has developed over the years. Their customers know Integrity is going to give them an honest estimate and perform excellent work. They feel comfortable bringing the trailer in, saying, “Tell me what it’s gonna cost,” and then paying up.
Ah, every shop owner’s dream.
COMPETING SHORTAGES
The trailer world is kind of in a strange place right now for reasons that will be familiar to all our readers: the tech and parts shortages. A lot of Integrity’s focus these days is getting all the parts they need in order.
“When we do large jobs, what’s really key to making them successful and profitable is making sure we have everything we think we might need on hand before we start tearing into it,” Glen tells us. “When we tear into a big job like that, it’s taking up a big chunk of our floor space, and if we don’t have everything and can’t keep that job moving along … it can get real expensive in a hurry.”
Like many shops, they’ve adapted. They perform a thorough inspection process before ordering parts and pulling a trailer into the bay in the hopes of minimizing any surprises. Parts, of course, remain a wild card; sometimes they show up on time, sometimes it takes weeks, and sometimes you order one part, but a different one shows up.
“The rules have definitely changed,” Glen says. “Just-In-Time is no longer a good model to live by. It was for years … but we can’t count on that any longer. We have to make sure we have more inventory on hand, and we’ve been reaching further and wider for things.”
(They’re not the first shop to mention stocking up on inventory, by the way. Zeb Todd gave us the rundown on parts hoarding earlier in the week, and it’s interesting to see other operations trying to keep more parts immediately on hand. We will note that it’s often more challenging with trailer parts because many of them are so darn big.)
Things get really complicated when they’re dealing with trailers that most of us would assume were lost causes. Glen remarks that they’re fixing a lot of things that probably wouldn’t have gotten fixed before—including trailers that have been in some pretty nasty wrecks. Because not only does the trailer world face a tech shortage and a parts shortage, but also an overall, well, trailer shortage.
Yep.
Trailer manufacturers suffered from the same problems as other industries. Worker shortages and lockdowns meant new trailers could not be built at their usual rate. They’re trying to get back up to speed, but they still have a way to go before catching up.
“At one point, the factories for new trailers were backlogged for a year, at least,” Andrew says. They were also limiting orders.
The lack of new trailers means older trailers—some of which have definitely seen much better days—are being refurbished and sent back into service. Is it a lot of work? Yup. But it’s the only option when manufacturers are running a year or more behind.
NO TRAILERS, NO TOYS
Here’s the thing about the trailer world: it’s not going anywhere.
People just don’t think much about trailers. But they’re just as important as the trucks that haul them from Point A to Point B; like we said up top, the trailer is what actually holds all the stuff. In short, a world without trailers is not a world where you get all your Amazon Prime packages in anything resembling a timely manner.
So yeah, it’s an important vertical. And all the competing shortages mean there’s plenty of work—challenging work, but often very satisfying.
Glen describes Integrity’s trailer techs as true craftsmen, who take a great deal of pride in taking a torn-up trailer and making it look and feel brand-new again. And why not? They’re performing an important service by maintaining a pretty big portion of the supply chain—actually, we’ll go so far as to say a huge portion of the supply chain.
So, next time you see a trailer on the freeway, remember how much work goes into maintaining them, and like us, be a little awed that humans can actually fix them.