Automate Construction Equipment Repairs with Inventory Systems
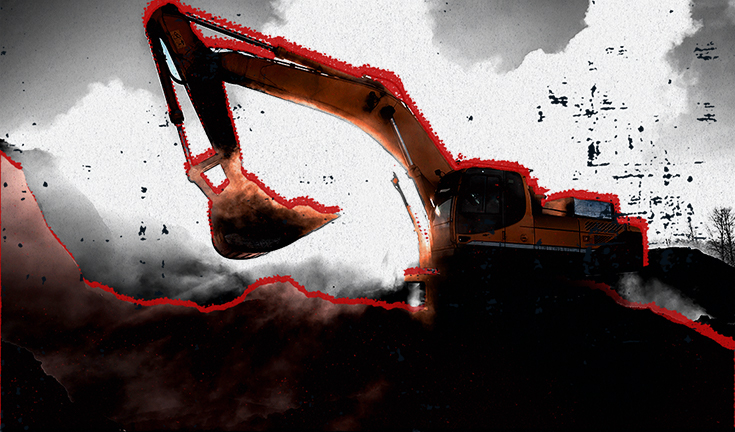
The introduction! It’s an essential part of any blog—including the article you’re reading at this very moment. And as luck would have it, this blog is about using automated inventory software to streamline your equipment repair shop. Why is that lucky? We don’t know!
*deep breath*
Anyway: if you’re in charge of a construction equipment repair shop, you know how chaotic things can get in these environments. It can be easy to lose track of your inventory levels—especially if you’re tracking this information by hand. Your shop could run into serious issues if you don’t closely monitor the parts you have in stock.
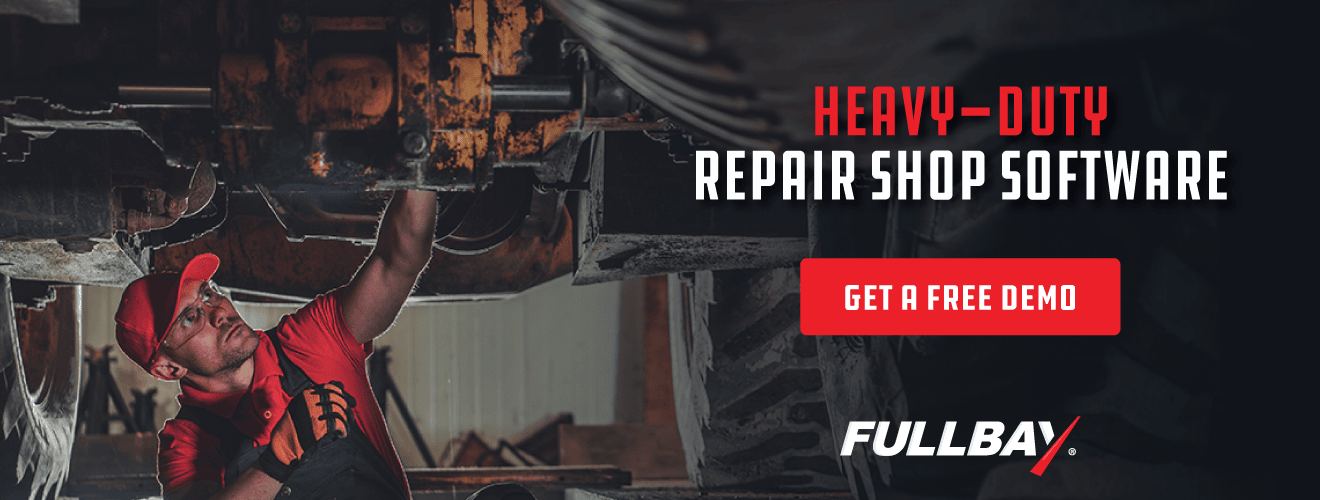
Fortunately, modern inventory programs can make tracking and reordering inventory less complicated than ever. In this article, we’ll explain how choosing the right construction inventory management system can streamline your shop’s operations.
What Is Construction Inventory Management?
If you run a diesel truck repair shop or any other business dealing with heavy equipment, you should always have a certain number of components in stock. However, there’s always a chance that parts could go missing, get stolen, or run out. To prevent issues like these, your business needs an inventory management system.
Technically, the term “inventory management system” can describe any type of part counting or tracking. But these days, you can safely assume that this phrase refers to programs that automatically track individual components and stock levels. Since the best digital inventory management systems are powerful, affordable, and easy to use, these programs have become an industry standard over the years.
Meanwhile, construction inventory management systems are designed to track components on construction sites and in construction equipment repair shops. That’s important because construction-centric heavy equipment shops often struggle to track parts across multiple sites. A high-quality inventory management system can easily record part locations, making this problem a thing of the past.
How Construction Inventory Systems Can Improve Construction Site Efficiency
Construction equipment repair shops should be ready for anything, and construction inventory systems can help. Because these systems take your exact use case into account, they’ll be able to manage a wide variety of tools and equipment as soon as you set them up.
If you choose the right software for this job, your techs won’t have to waste time tracking inventory by hand, either. Today’s inventory programs can automatically monitor your shop’s stock levels, predict your part-related needs, and send reorder reminders when you’re running low on components.
When you’re in the market for a new construction inventory management system, it’s wise to prioritize features like barcode scanning, cloud accessibility, and real-time reporting. These capabilities can eliminate common sources of inefficiency around your shop, enhancing its operations while minimizing downtime.
What Are the 4 Types of Inventory Management Systems?
When it’s time for your shop to order components, you’ll want to avoid buying too few (or too many) parts. These strategies for managing your inventory can help:
1. Just-In-Time
The just-in-time (JIT) strategy is all about minimizing stock levels. Instead of keeping massive numbers of parts in stock, shops using this system rely on their suppliers to deliver parts when they actually need them. As a result, they can:
- Cut down on physical space dedicated to inventory storage
- Avoid clutter around work sites
- Keep holding costs under control
- Lower the possibility of stockouts/overstocking
JIT isn’t a perfect system—if demand for a given part spikes unexpectedly, you may have to wait for a replacement. However, the advantages this system can deliver make it ideal for shops that go through a ton of parts.
2. Economic Order Quantity
When your shop optimizes its economic order quantity (EOQ), it will greatly reduce its risk of encountering inventory-related problems. This term refers to the ideal part order for your business—an order that contains enough parts to keep up with demand while keeping inventory-related expenses under control.
To find your EOQ, you’ll follow the formula Q=√ (2DS/H) . Here’s a quick breakdown of what these variables mean:
- D stands for your shop’s demand in units (normally on an annual basis).
- S stands for your order cost per purchase.
- H stands for your per-year, per-unit holding costs.
- Q stands for your EOQ in units.
If you’re wondering how to put this formula to use, a real-life example might be just what you need to get started. Unfortunately, Fullbay’s blogging team is legally prohibited from doing math, so we can’t help you with that. Just stare at the letters until they make sense!
(One more thing: it’s important to remember that the EOQ formula assumes that your shop’s parts demand will never change. If you’re interested in expanding your business any time soon, you’ll need to use this formula alongside other inventory management methods to get a more complete picture of your shop’s inventory needs.)
3. ABC Analysis
In the ABC analysis system, shops use information on part demand, cost, and risk to divide their components into three categories:
- Class A parts are the most important, in-demand components in a shop’s inventory.
- Class B parts fall between Class A and Class C components in terms of significance.
- Class C parts are the least crucial components a shop has in stock.
Admittedly, the process of separating your shop’s parts into multiple categories can be time-consuming. But when this work is complete, you’ll find it easier to forecast inventory demands and use your resources wisely.
4. FIFO and LIFO
The words “Fifo” and “Lifo” might sound like the worst possible names for a pair of dogs, but that’s not what these terms mean. Instead, they’re acronyms for different types of inventory valuation: “FIFO” stands for “First In, First Out,” and “LIFO” stands for “Last In, First Out.”
If your shop uses the FIFO inventory management system, you’ll assume the oldest parts you have in stock are sold first. On the other hand, the LIFO method assumes that the newest parts in your shop’s inventory are sold first.
Since heavy-duty parts have a limited shelf life, LIFO probably isn’t the best fit for your shop. Instead, you’ll want to use FIFO, which should align more closely with how your techs actually use components.
What Are the 3 Inventory Control Systems?
While it’s easy to think that inventory management systems and inventory control systems are basically the same thing, there’s still an important difference between these categories. Unlike inventory management systems, inventory control systems are all about tracking and recording your current inventory levels.
To monitor parts levels and maintain accurate inventory levels, you’ll need the help of one of these systems:
1. Perpetual Inventory System
If business is booming at your construction equipment repair shop, there’s a good chance that parts are flying off the shelves. But in this situation, counting your stock levels by hand may be nearly impossible.
That shouldn’t be a problem when you have access to a perpetual inventory system. These systems automatically update your shop’s inventory levels based on info from your point-of-sale system, letting you know exactly when a part leaves your shop’s inventory.
2. Periodic Inventory System
On the other hand, periodic inventory systems represent an “old-school” approach to parts management. Though it may seem like physically counting inventory is “good enough” for your shop, this approach could cause serious issues for your business.
You don’t need us to tell you that construction equipment repair shops are fast-paced, busy environments. On the other hand, manual inventory counts are an inherently slow process—and they may not be able to give you the information you need when you need it. Plus, you could run into even worse efficiency problems if an employee accidentally miscounts parts.
3. Barcode and RFID Systems
Human error is the enemy of efficiency, so your shop’s inventory system should keep manual input to the bare minimum (even when it comes to something as “simple” as logging part locations). That’s why it’s smart to adopt an inventory system that utilizes barcode and RFID technologies.
When your shop uses a barcode-based inventory control system, each part you use will have a corresponding barcode. Meanwhile, an RFID-powered inventory system relies on active RFID tags (tags with an internal power supply) or passive RFID tags (tags with no power source of their own). Both of these tracking methods allow employees to update part locations and other data points with a quick scan, which can go a long way toward simplifying your shop’s inventory management process.
Maximize Your Shop’s Efficiency With Fullbay
The conclusion! That’s the article section that you’re at right now. That is to say, the section you’re reading. You’ve done a great job making it to the end of the blog, and we’re all very proud of you. And now, it’s time…for the sales pitch.
Like any piece of business software, a construction inventory management system is an investment for your shop. Because of that, you shouldn’t buy just any program for this job. Instead, you should try to find software that delivers efficiency-boosting features like real-time inventory tracking, barcode/RFID compatibility, service order generation, and mobile accessibility.
Fortunately, you’ll get all these features and more when you choose Fullbay—and that makes our inventory management system the perfect choice for businesses like yours. Find out what we can do for you by scheduling a demo today!