9 Advantages of a Cloud-Based Inventory Management System
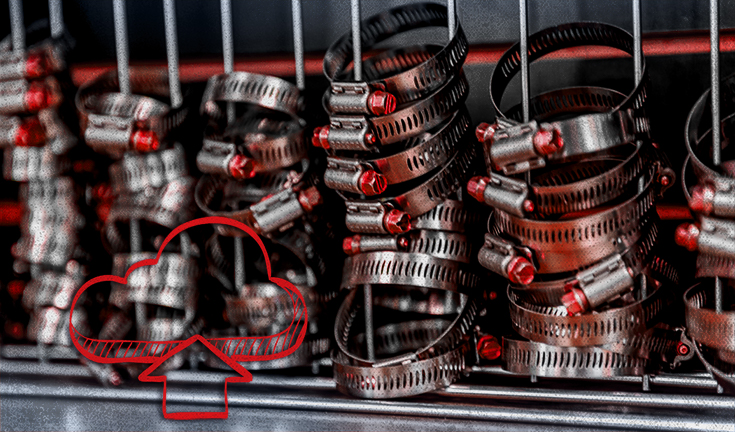
Has anyone ever told you that you have your “head in the clouds?” Unfortunately, this saying isn’t usually a compliment. Instead, it describes people who are distractible, unrealistic, and…sorry, what were we talking about?
Oh, yeah: as it turns out, the opposite is true for software in the cloud. Since cloud-based inventory systems can be highly accessible and extremely powerful, they’re an extremely practical choice for heavy-duty repair shops looking for inventory management software.
If you’re ready to manage inventory like a pro, we can help. Here’s what you need to know about the benefits of adopting a cloud-based inventory management system (and how to choose one of these programs for your business).
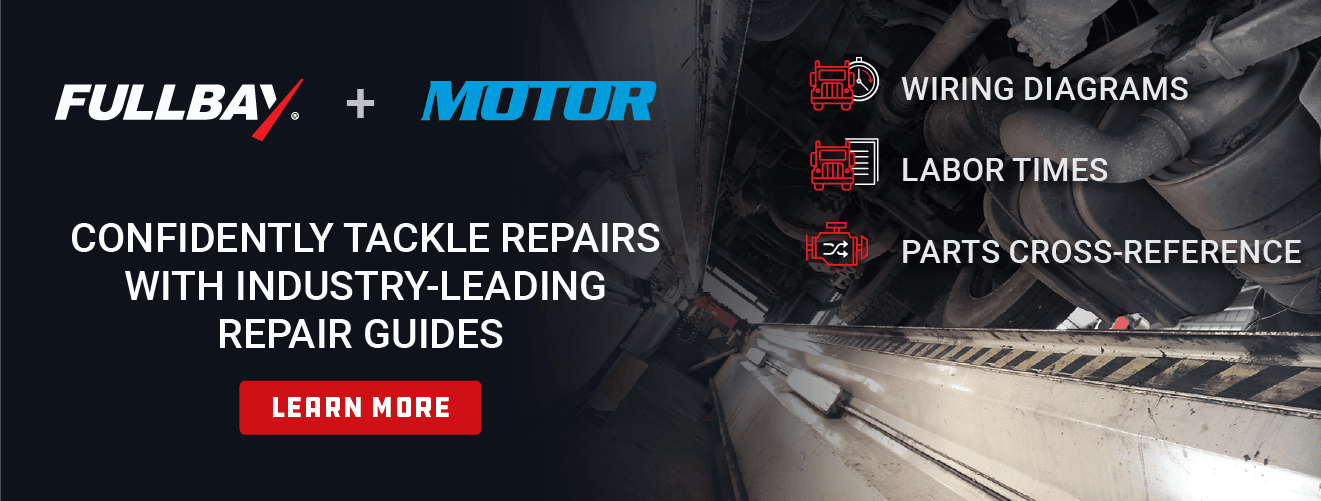
What is a Cloud-Based Inventory Management System?
Quick—grab the nearest calendar and check what year it is! Notice how this number starts with “20” and not “19?” That means it’s time for your shop to stop tracking inventory by hand. Along with its obvious efficiency issues, manual inventory tracking can significantly increase your shop’s risk of recording inaccurate inventory data.
Today’s best inventory management systems simplify inventory-related tasks like part level tracking and component reordering, but not all modern inventory systems are created equal. If your shop relies on an on-site solution for this task, you could run into some unexpected problems. For example, you may find yourself dealing with inconsistent part counts and have trouble keeping up with your growing inventory. This is especially true if you operate out of multiple locations or do mobile truck repairs.
Choosing a cloud-based inventory system is an easy way to avoid these difficulties. Since these systems run on remote servers and are accessible through the internet, you won’t have to invest in expensive hardware to use them. Instead, your techs will be able to view inventory information on the computers and mobile devices they already use.
9 Advantages of Cloud-Based Inventory Management for Multi-Location Repair Shops
When your chain of heavy equipment repair shops adopts the right cloud-based inventory management system for its needs, you’ll benefit from:
1. Real-Time Inventory Tracking
Whether your heavy-duty shop has one location or a dozen, you’ll want constant access to information on your stock levels, purchase orders, and more. In today’s fast-paced work environments, “traditional” methods won’t be enough to give you the up-to-the-minute inventory updates you need.
This means that real-time, cloud-based inventory tracking is a must for today’s shops. When you and your techs always have up-to-date information on stock levels and can easily reorder the parts you need, you’ll be able to keep repair delays to a minimum. That’s particularly true when you can access this system anywhere thanks to mobile compatibility.
2. Centralized Data for Multi-Location Operations
Inventory tracking is one of the most significant challenges associated with running a multi-location repair shop. If you try to manage inventory for each shop in your chain separately, you could have trouble making your numbers add up—especially if you’re tracking part levels by hand or through an assortment of spreadsheets.
The good news is that this won’t be an issue when you can access inventory data for all of your locations from a single platform. By using this method for inventory management, you’ll never have to worry about one shop’s inventory count not matching another shop’s information. Along with that, centralized data will make it easier to transfer inventory from one location to another.
3. Improved Customer Satisfaction
If your workers always know where parts are located in one of your shops, they won’t have to spend valuable time looking for these components. At the same time, this information can lower your risk of running out of parts—and both of these advantages can help you keep customers happy by avoiding job delays.
When you start using a cloud inventory system, you should also get access to in-depth, real-time data on your shops’ operations. By putting this data to good use, you’ll be able to offer complete transparency to your clients regarding job scheduling.
4. Optimized Stock Levels
Understocking parts can cause problems for any shop: if you run out of the components you need, you’ll have to put jobs on pause and risk aggravating your customers. But if you overstock parts, you could waste storage space at your locations and face unnecessarily high carrying costs.
Instead, you’ll want to optimize your business’ stock levels with a cloud-based inventory management system. Since these systems offer modern features like real-time part tracking and automated reorder reminders, you’ll be able to use your warehouse space as efficiently as possible. At the same time, these systems deliver powerful demand forecasting that can help you keep carrying costs under control.
5. Supply Chain Visibility
The best cloud inventory systems deliver meaningful improvements at each step in a diesel truck repair shop’s supply chain. As part of that, these programs can integrate directly with your suppliers—giving you up-to-date info on part availability and estimated shipping times.
Since cloud-based inventory management can improve coordination between your business, its suppliers, and parts manufacturers, you’ll have a much easier time ensuring the components you need are always in stock. And thanks to the streamlined purchasing and receiving processes these systems deliver, your shop’s reordering process will be smoother than ever.
6. Enhanced Reporting and Analytics
When you have access to accurate information before making a decision about your repair shop branches, you’ll have much better odds of making the right choice. That definitely applies to part ordering—and modern inventory software can enhance the reordering process by sharing insights on purchasing habits, stock usage, and sales trends at your shops.
Thanks to these accurate part demand forecasts, you’ll be able to lower your risk of component shortages without ordering too many parts. Additionally, your inventory system should deliver customizable reports on stock movement, repair orders, and the overall health of your inventory.
7. Reduced Administrative Burden
Even if you can track your shop’s inventory by hand, that doesn’t mean you should. This process takes a lot of time—time your shop’s employees could spend doing something more productive.
By automating your inventory counts, purchase orders, and receiving logs, you’ll avoid manual data entry (and the human error that comes with it). Automated inventory systems can also simplify compliance and audit tracking.
8. Scalability
As your shop adds new locations and starts buying more parts, you’ll need an inventory system that can grow alongside it. While it might be easy to assume any digital inventory system will be up to this challenge, that isn’t the case in practice.
If you use an on-premise solution for inventory tracking, you may need to invest in pricey hardware upgrades to meet your business’s changing needs. On the other hand, cloud-based systems can provide whatever inventory services your shop is looking for.
9. Remote Access
Checking stock levels, reordering parts, and updating inventory data are vital tasks—and they shouldn’t be locked to a single workstation in your shop. Instead, your employees, managers, and techs should be able to complete these jobs wherever they are by accessing your inventory system remotely.
While any heavy-duty shop can benefit from remote inventory system access, this is especially important for shops that require a certain level of flexibility. If your business regularly works on mobile repairs or relies on off-site management, finding an inventory system that delivers this advantage should be one of your highest priorities.
Choose the Best Cloud-Based Inventory Management System
When your shop has access to the right cloud-based inventory management system, you’ll enjoy the benefits listed in this article and more. However, not every piece of inventory management software on the market will deliver all these advantages.
Instead, you’ll need to do some research to pick the right cloud-based inventory program for your heavy-duty shop. This will be a grueling process, forcing you to spend weeks or even months looking f–
Just kidding! If you’re reading this article, you’ve already found the perfect inventory software for your business. Fullbay takes pride in offering cloud-based inventory systems that deliver real-time inventory updates, powerful reporting features, and centralized data (just to name a few benefits). Get your head out of the clouds and schedule a demo today!
<script type=”application/ld+json”>
{
“@context”: “https://schema.org”,
“@type”: “Article”,
“mainEntityOfPage”: {
“@type”: “WebPage”,
“@id”: “https://www.fullbay.com/blog/9-advantages-of-a-cloud-based-inventory-management-system/”
},
“headline”: “9 Advantages of a Cloud-Based Inventory Management System”,
“description”: “The article highlights the benefits of cloud-based inventory management systems for repair shops, including real-time data access, cost efficiency, scalability, improved accuracy, strong security, seamless integration, automatic updates, disaster recovery, and environmental advantages, leading to better efficiency and reduced costs.”,
“image”: “https://www.fullbay.com/wp-content/uploads/2024/12/Blog-header_Cloud-Based-Inventory.jpg”,
“author”: {
“@type”: “Person”,
“name”: “Suz Baldwin”
},
“publisher”: {
“@type”: “Organization”,
“name”: “”,
“logo”: {
“@type”: “ImageObject”,
“url”: “”
}
},
“datePublished”: “2024-12-11”
}
</script>